Resortecs x Sioen: The start of a European consortium for workwear textile waste management
Resortecs, a leader in textile eco-design and end-of-life waste management, partners with Sioen, a global leader in technical textiles and protective clothing, to create workwear that combines durability with circularity. This collaboration is a major milestone in developing workwear that meets the highest safety standards while being designed for disassembly and recycling at the end of its lifecycle.
Under the agreement, Sioen will be integrating Resortecs’ Smart Stitch™ heat-dissolvable threads into its workwear production. This enables the creation of eco-designed garments that can be efficiently disassembled and recycled without compromising quality, comfort, nor protective functionality. Resortecs, on the other hand, will offer its comprehensive textile waste management service, that includes the disassembly and sorting of the discarded and returned textile products, as well as facilitating the recycling of the sorted textile materials.
Bart Vervaecke, CEO of Sioen’s Protective Clothing division, commented:
“Sioen together with Resortecs makes a big step in ready-to-dismantle garments with this cooperation. We are proud that with our support we can enable Resortecs to install their EU-based disassembly line. Resortecs’ technology will play an important role as a fully integrated part of our sustainable strategy at Sioen, drastically improving the end of life solution for our garments.”
The beginning of a textile waste management circularity consortium in Europe
This collaboration lays the foundations of a Resortecs-led consortium in the Benelux and France regions for end-of-life textile waste management of workwear. The consortium will unite the efforts of workwear manufacturers, recyclers, government agencies, and Resortecs, to facilitate an operationally optimised and financially viable circular textile waste-management solution for complex apparel.
At the heart of the consortium is a Smart Disassembly™ line, with an annual processing capacity of 3000 tons, that will be placed and operated in Belgium by Resortecs by the end of 2025. The Smart Disassembly™ pre-processing line will integrate with existing sorting and collection infrastructure, as well as current and upcoming recycling technologies.
Resortecs’s holistic waste management solution uses an innovative technology to solve a critical challenge in textile recycling. By automatically eliminating trims that block recycling and reclaiming double the amount of a product’s textile content, up to 15x faster, Resortecs facilitates circularity on an industrial scale. As a result, high-performance workwear, along with other textile products like mattress covers and fashion garments, can now be disassembled and recycled more effectively.
Workwear manufacturers operating in Belgium, Netherlands, Luxembourg and/or France can now take part in the consortium by simply producing their textile products with the heat-dissolvable Smart Stitch™ sewing threads. Once those textile products have reached their end-of-life, they are delivered to Resortecs for disassembly, sorting, and recycling. Get in touch to learn more.
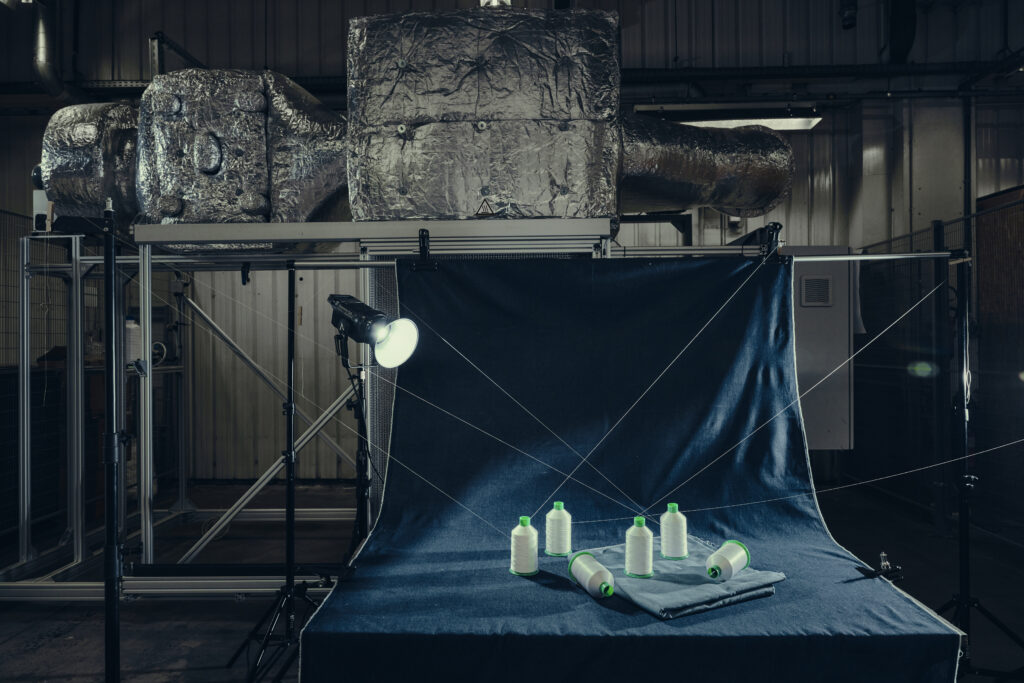
A new circular standard for protective textiles
This collaboration marks a crucial step towards setting circularity as the new standard in the protective clothing and technical textiles sectors, with the goal of producing over half a million of fully recyclable garments with Sioen in the coming 3 years.
Cédric Vanhoeck, CEO and co-founder of Resortecs, commented:
“As we drive circularity in protective textiles, we’re challenging industry norms. Many believe that circular design can’t align with safety standards, but we’re proving otherwise.This collaboration shows how innovation is key in the sector for building a more sustainable future without technical compromises.”
By combining Sioen’s expertise in protective gear with Resortecs’ cutting-edge Design-for-Disassembly technology, the partnership is setting a precedent for workwear that protects both workers and the environment.
“It’s galvanising to see one of the biggest workwear players in Europe supporting our efforts in creating a pan-European network of disassembly and pre-processing infrastructure. We are actively looking for other market leaders in other European regions such as DACH, Iberian Peninsula, and Scandinavia with whom we share the same vision in rejuvenating the European textile industry”, added Cédric Vanhoeck.
About Resortecs
Resortecs® offers pre- and post-consumer textile waste management services for the fashion, workwear, bedding and automotive industry. The company offers heat-dissolvable stitching threads (Smart Stitch™) and thermal disassembly systems (Smart Disassembly™) that enable easy, automated textile recycling on an industrial scale. Resortecs’ mission is to lead the textile industry towards full circularity by facilitating Design-for-Disassembly (DFD).
About Sioen
Sioen is a global leader in technical textiles, colouring solutions and protective clothing, providing high-performance solutions for a wide range of industries, including workwear, firefighting, military, and forestry. Dedicated to innovation, Sioen combines advanced materials and cutting-edge designs to ensure maximum safety and durability, all while striving to promote sustainability through the development of circular products.
More information about Sioen can be found online at: https://sioen.com/en
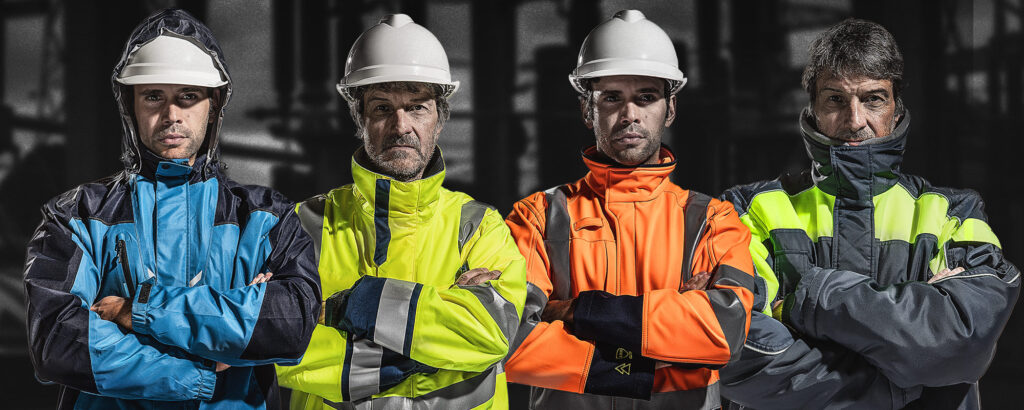
As the global community continues to grapple with the urgent need for sustainable solutions, the textile industry stands at a critical crossroads. With increasing awareness of environmental degradation and resource depletion, there is a growing imperative to reevaluate traditional manufacturing practices and embrace more sustainable alternatives. At the forefront of this movement is the concept of eco-design, which emphasizes the integration of environmental considerations into product development processes.
As the European Union discusses the EU Ecodesign Directive and other measures to boost textile circularity, it is clear that the environmental impact of textile products has made fashion one of the region’s top priorities in the circular transition. On average, an EU citizen consumes 26 kg of textile and generates 11 kg of waste each year. Yet only 1% of the material used in textile production is recycled — the remaining 99% is landfilled or incinerated.
Objective
In alignment with the principles of eco-design for sustainable products (ESPR), this study seeks to estimate the achievable target for recycled content in textile products, specifically apparel, that are placed on the European market. The focus is on utilizing recycled content sourced from collected textile waste within Europe over the next decade.
By leveraging recycled materials, manufacturers can reduce reliance on virgin resources, minimize waste generation, and mitigate the environmental footprint of their products. Through a comprehensive analysis of industry trends, consumer preferences, and regulatory frameworks, this report aims to provide insights and recommendations for establishing meaningful recycled content targets that promote sustainability without compromising product quality or performance.
Methodology
The study aimed to assess the potential feedstock available from collected textile waste in Europe, both with and without pre-recycling preparation such as disassembly. It investigated the amount of attainable feedstock achievable under current conditions, as well as the additional feedstock that could be obtained if pre-recycling preparation methods like disassembly were implemented.
The following assumptions were considered in the calculation:
• Global Market Size: The global market for textile products is estimated to consist of 116 billion pieces annually. Of these, the European market represents 28%, equivalent to 32.5 million pieces, with an average weight of 300g per piece, totaling 9744 tons per year. This value is assumed to remain stable over the study period despite the growth potential.
• Monomaterial Fraction: Currently, monomaterial products constitute 22% of total fashion collections. It is anticipated that this proportion will increase due to eco-design requirements (ESPR), reaching 30% by 2035.
• Composition of Materials: PET accounts for 12% of the material composition, while cotton represents 40%. The recycling efficiency is estimated at 47% for PET and 49% for cotton, accounting for material loss during recycling processes such as melt spinning, twining/spinning, weaving, and confection.
• Disruptors and Multimaterial Products: Products made from mono-materials and containing recycling disruptors such as zippers, labels, and buttons comprise 69% of total fashion pieces7. Multi Material products constitute 9% of the total fashion pieces7.
• Textile waste collection rate: The average textile collection rate in Europe is currently estimated at 38% with the aim of achieving 100% with the mandatory textile waste collection.
Data Analysis
In the light of the waste framework directive WFD EC 2008/98 and the mandatory collection of separated textile waste the percentage of the collection rate is expected to increase from the present state of 38% to 60% in 2027, up to 80% in 2030 and 100% by 2035.
The mono-material fraction currently constitutes around 22% of the total garments in the EU market. With the implementation of eco-design requirements and the potential for garments to be designed as mono-material, eliminating the need for trims or multi-material components to meet performance and durability standards, this fraction is projected to rise to 30% by 2035. Accordingly, given the current collection rate of 38% of textile waste in Europe, the textile industry can procure 98 tons of polyester feedstock and 326 tons of cotton feedstock in 2024.
This volume of feedstock will be adequate to meet the requirement for 4% recycled content in new garments without necessitating any modifications to current practices or additional investments. With the aim of achieving collection rates of up to 100% in the EU, the potential feedstock obtainable from mono-material textile waste collected in Europe is anticipated to amount to at least 346 tons of cotton feedstock and 1152 tons of polyester feedstock. This could potentially translate into achievable recycled content targets of 14% to 15% by 2035, respectively.
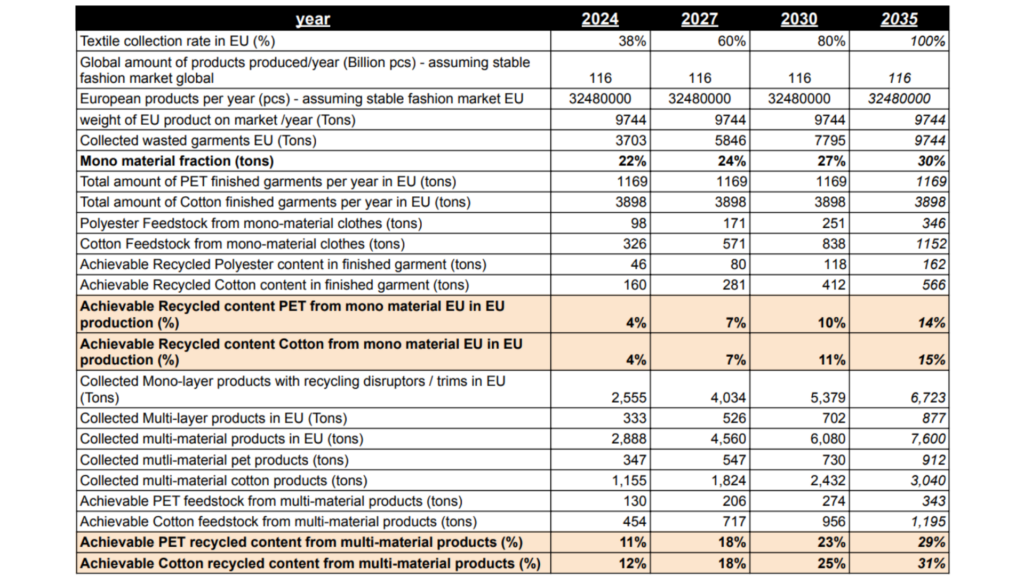
Table 1: Potential textile recycled content targets and their feasibility in the EU.
Tapping into multi-material textile products, which may consist of mono-material with recycling disruptors or multi-layer compositions, and assuming they are prepared for recycling through effective disassembly, the achievable PET feedstock is projected to increase from 130 tons in 2024 with a 38% collection rate to 343 tons in 2035 with a 100% textile waste collection rate. Consequently, the achievable PET recycled content from multi-material sources will range from g.
A similar trend is expected for cotton feedstock, estimated at 454 tons in 2024 and evolving to 1195 tons if 100% of multi-material apparel waste is collected and disassembled in Europe. This will result in achievable cotton recycled content ranging from 12% to 31%.
Combining the potential PET feedstock collected in Europe from both mono-material and multi material apparel products will result in 16% of achievable recycled PET target in 2024 with projection to increase to 45% by 2035, as demonstrated in Figure 1.
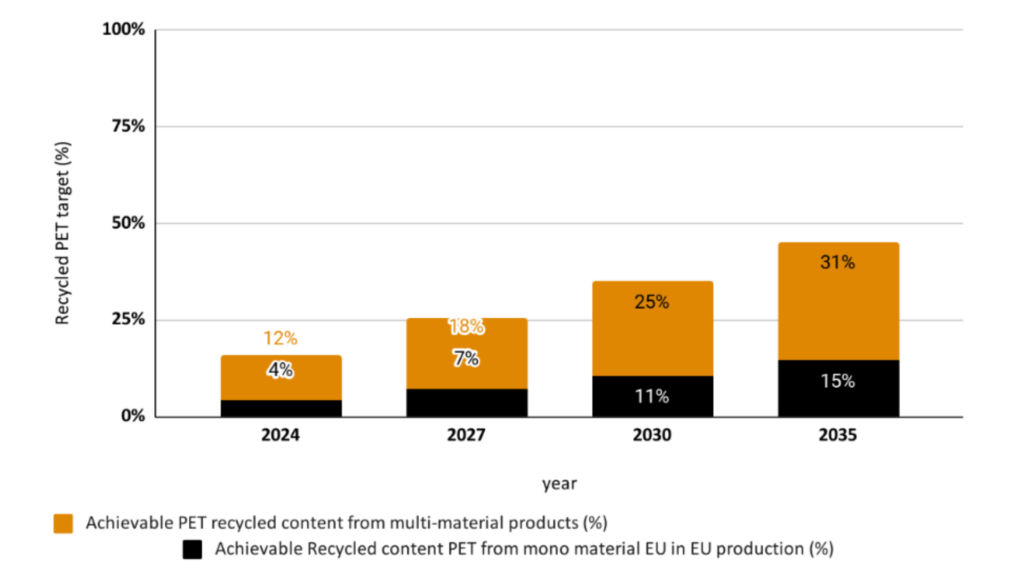
Figure 1: Achievable Recycled PET Content (%) from Mono-Material and Multi-Material Textile Waste Collected in the EU.
Combining the potential cotton feedstock collected in Europe from both mono-material and multi material apparel products will result in 39% of achievable recycled cotton target in 2024 with projection to increase to 43% by 2035, as demonstrated in Figure 2.
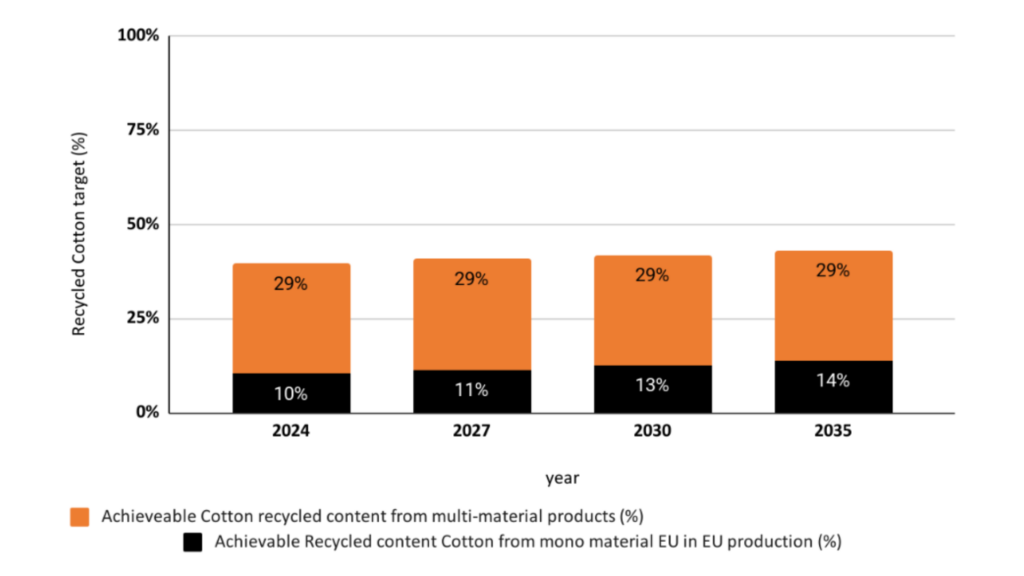
Figure 2: Achievable Recycled Cotton Content (%) from Mono-Material and Multi-Material Textile Waste Collected in the EU.
Conclusion
The study’s results underscore the tangible potential for achieving significant levels of recycled content in new apparel products. The min achievable recycled content target is 4% from mono-material garments without changing any current practices that could rise to 14% when 100% of textile collection rate is attained. By tapping into multi-material garments after preparation for recycling, a min achievable recycled content target is 11% with potential to rise to 31% when 100% of multi-material textile collection rate is attained. With careful management of current European textile waste, a realistic recycled content target of 15% is within reach. Looking ahead, as textile waste collection becomes mandatory and reaches 100% penetration over the next decade, the projected recycled content target could soar to an impressive 43%. It’s crucial to note that while market growth may amplify these volumes, our study prioritizes responsible production practices and expects products to have longer lifespans in the market, and it didn’t consider any market growth.
The study findings highlight the pivotal role of the disassembly process, exemplified by Resortecs’ design for disassembly solution. Effective preparation of products for recycling will unlock higher volumes of feedstock with the necessary purity for textile-to-textile recycling processes. This optimization not only streamlines the sorting process and increases recycling yields, but also generates financial benefits for sorters and recyclers. Moreover, it significantly mitigates environmental impact by reducing waste generation and curbing the need for new material sourcing. This emphasizes the imperative for defining eco-design requirements that foster an enabling environment for textile-to-textile recycling, thereby actualizing the waste hierarchy. Such an environment must prioritize pre-recycling techniques like disassembly and set ambitious recycled content targets that not only reflect high percentages but also ensure the origin of recycled content is sustainable and traceable. This holistic approach is essential for driving meaningful progress towards a circular and sustainable textile industry.
Sources
1. 2009/125/EC
2. Textiles in Europe’s circular economy, EEA, 19 Nov 2019.
3. A new textile economy: redesigning fashion’s future (Ellen MacArthur Foundation) – Circular Fibers Initiative analysis.
4. Statista – Apparel Europe, and Apparel Market Worldwide.
5. Global apparel market: The revenue of the global apparel market was calculated to amount to 1.53 trillion U.S. dollars in 2022 while Apparel – Europe: In 2023, the revenue in the Apparel market in Europe is estimated to be US$474.40bn hence the EU market share of the global apparel market is 28%.
6. Resortecs internal calculation for an average garment weight.
7. Refashion, Characterisation study of the incoming and outgoing streams from sorting facilities report, 2023.
8. Fashion For Good, Sorting for Circularity Report, 2022.
9. Recycling efficiency was estimated on analysis of current recycling technology and industrial discussions with developing recycling technologies at lower TRL.
10. EU exports of used textiles in Europe’s circular economy – Feb 2023.
11. European Directive ((EU) 2018/851) amending Directive 2008/98/EC
In recent years, a significant transformation has been underway in the world of finance, with Environmental, Social, and Governance (ESG) considerations taking center stage. This shift is not merely ideological but stems from a growing recognition among financial decision-makers that sustainable practices are not only ethically sound but also financially lucrative. As corporations face mounting pressure to address societal challenges, a parallel movement is unfolding, propelling the circular economy into the spotlight as a lucrative investment opportunity. This change can be attributed to various factors.
1. In a shifting landscape, financial decision-makers with aspirations beyond mere monetary gains are demanding tangible actions from corporations. The prevailing sentiment acknowledges that Environmental, Social, and Governance (ESG) considerations not only serve as risk indicators but also foster enduring expansion and cultivate novel avenues of value by supporting entities that are actively addressing the current social challenges. Insights from Opimas and the Global Sustainable Investment Alliance unveil a staggering surge in ESG investments, exceeding $40 trillion in 2020 from a baseline of $23 trillion in 2016. Projections by Deutsche Bank underscore an imminent paradigm shift, suggesting that a substantial 95% of assets under management, equating to $130 trillion, will align with ESG principles by 20301.
2. Concurrently, governmental bodies, regulatory authorities, and central banks are realigning public expenditures and policy frameworks to facilitate the shift toward an all-encompassing, environmentally conscious circular economy. The configuration of investment opportunities is transforming, evolving beyond being a fad to manifest as a substantial and widespread movement1.
“Over the last 18 months, funds that focus on environmental-focused investments have outperformed almost all other forms of index, some people will call that a momentum investment. I would call that a sea change, I would call that a recognition that we have to move forward fast. Larry Fink, CEO, BlackRock 13 August 20211.
These factors have resulted in a substantial upswing in dedicated financing activities to offer investors a wider array of options to align their portfolios with sustainable and circular practices, leading to the emergence of different debt and equity instruments tailored to support circular economy initiatives.
Among these financial instruments are public equity funds (their number increasing from 2 in 2018 to 13 in 2021 including funds from the world’s largest investors BlackRock, BNP Paribas, Credit Suisse, and Goldman Sachs), corporate and sovereign bonds, venture capital, private equity (tenfold increase in the number of private market funds from 2016 to H1 2020), and private debt. Financial institutions have also actively participated in driving circular economy initiatives through bank lending, project finance, and insurance solutions2.
One example of the financial sector’s commitment to sustainable and circular practice is the exceptional growth in assets under management (AUM) in public equity funds centered around the circular economy. Between December 2019 and the first half of 2021, AUM skyrocketed from $0.3 billion to an astounding figure exceeding $9.5 billion at the end of November 2021, demonstrating a 28-fold in less than 2 years2.
Additionally, between December 2019 and December 2021, the issuance of corporate and sovereign bonds centered around the circular economy witnessed an impressive 5-fold increase. Over the past three years, a minimum of 40 such bonds were issued, highlighting the growing interest and commitment towards financing circular economy initiatives2.
Last, but not least, index providers are diversifying their offerings to encompass the circular economy domain, unveiling a host of new specialized products. Here are a few examples:
— Solactive has taken the lead by introducing an index with a focus on the sharing economy.
— Morgan Stanley Capital International (MSCI) has entered the scene with its index that highlights the circular economy and renewable energy.
— ECPI group has launched the Circular Economy Equity Leader Index, designed to capture companies excelling in various circular economy aspects3.
This remarkable financial mobilization highlights the confidence of stakeholders that the circular economy is not just an ethical choice but also an increasingly lucrative investment opportunity.
That confidence is also supported on the individual level. Naturally, many investors choose to invest in the circular economy because it is the right thing to do. However, it becomes obvious that increasingly, investors recognize the financial potential of such investments. Roughly one-third of investments in the circular economy in Europe, the Middle East, Africa, Asia, Australia, and North and South America are recognising the increasing returns4.
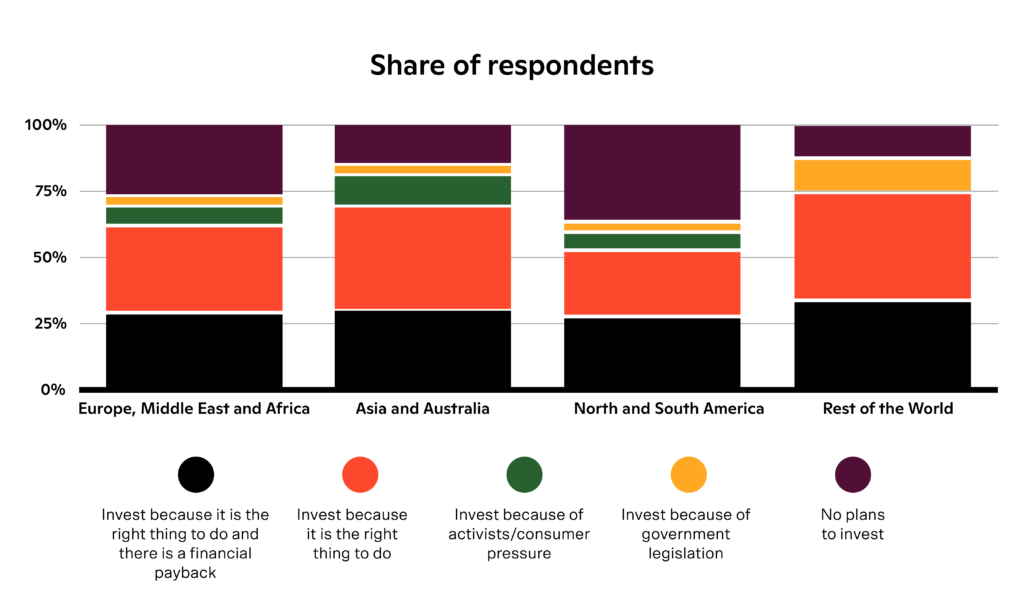
The rising confidence from financial institutions and individuals is not without support. A recent analysis by Bocconi University of 200+ European publicly listed companies supports the idea that circularity is the new winning strategy for investors looking to de-risk their investments and deliver superior risk-adjusted returns2.
The circular economy as a strategy to de-risk debt
In recent years, it has become increasingly clear that factors such as climate change, other climate-related crises, rising geopolitical tensions, and other societal challenges pose significant investment risks, and the financial sector is recognizing that. All actors in the financial system should work towards avoiding a climate-driven ‘Minsky moment’.
The recent analysis highlights that the more circular a company is the lower the risk of defaulting2. A 0.1 increase in Circularity Score (scoring developed by Bocconi University and Intesa Sanpaolo) is responsible for the reduction in the probability of default on debt by 8.63% (one-year timeline) and by 4.93% (five-year timeline)2.
The circular economy as a strategy for superior risk-adjusted returns
The same analysis concludes that the more circular a company is, the higher the risk-adjusted returns it generates on investment2.
Public equity funds with circular economy as a sole or partial investment focus on average performed 5.0 percentage points better than their Morningstar category benchmarks in the first half of 20202.
Potential drivers of these circular economy benefits include:
— a focus on design and business model innovation and diversification
— achieving greater resource decoupling
— anticipation of stricter regulation
— changing customer preferences
— resource scarcity
As the world grapples with pressing environmental and social challenges, the circular economy emerges not only as a solution but also as a lucrative investment opportunity. By embracing sustainable practices and innovative business models, investors can not only contribute to a more resilient and equitable future but also reap substantial financial rewards. In an era where the intersection of profitability and sustainability is increasingly recognized, the circular economy stands poised to redefine the landscape of finance for years to come.
Sources:
1 Mark Carney, Unlocking the Value of the Circular Economy, https://ellenmacarthurfoundation.org/articles/unlocking-the-value-of-the-circular-economy, August 2021.
2 Bocconi University, Ellen MacArthur Foundation, Intesa Sanpaolo (2021), The circular economy as a de-risking strategy and driver of superior risk-adjusted returns, http://www.ellenmacarthurfoundation.org/publications.
3 Mara Steinbrenner, Financing Circular Economy, https://neosfer.de/en/financing-circular-economy/, September 2022.
4 Martin Placek, Circular economy investment motives and decisions worldwide in 2019, by
region, https://www.statista.com/statistics/1182841/circular-economy-investment-decision-region/, April 2022.
With the tightening European legislation on waste management and investment in the circular transition gaining traction, it becomes clear that circularity is no longer a buzzword, it’s a necessity for those who want to stay competitive. For the ones who don’t recognize the ongoing shift, this should serve as a wake-up call: Circularity is the new standard of doing business and first-movers are already reaping the benefits.
For the past years, the circular economy has already instigated transformative shifts across industries. In the fashion sector, for example, clothing resale is projected to surpass fast fashion by 2029, while the realm of plastics and consumer packaged goods is witnessing the metamorphosis of profit pools throughout the value chain, driven by mounting regulation, public expectations, and innovative recycling technologies1.
Governments are propelling this transformation, exemplified by the circular economy’s integral role in the European Green Deal, alongside circular economy roadmaps and regulatory measures established in nations like China, Chile, and France. As a result of this and other driving factors of circularity, the use of circular materials in the EU increased by roughly 41% between 2004 and 2021, accounting for 11.7% of total material use in 20212.
The Concept of a Circular Economy
According to McKinsey, approximately 63% of potential emissions reduction in the fashion industry is estimated to come from the use of cleaner energy sources3.
All of the other 37% of emissions reduction, however, necessitates innovative strategies: this is where circularity comes in. Processes encompassing prolonged product life cycles, shifts in consumer behaviors, adoption of circular business models, curbed overproduction, increased integration of recycled materials, and other circular economy principles could contribute immensely—up to 654 million metric tons of emissions reduction in the fashion industry by 2030, effectively bridging the emissions reduction gap. This approach can be similarly applied across various consumer goods industries3.
Within a circular economy framework, four pivotal loops support the extension of product life cycles: repair, resale/rental, refurbishment, and recycling.
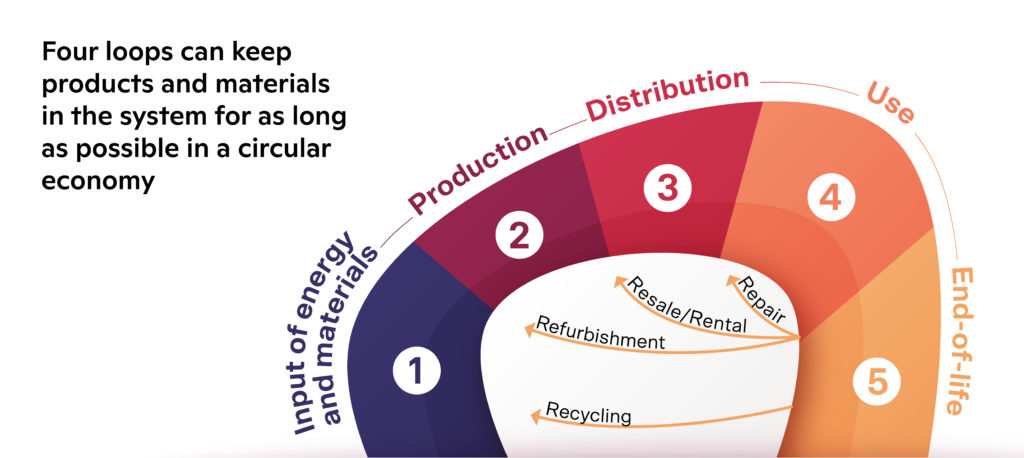
Circularity is the Future Standard of Doing Business
It is clear that the circular economy is driving transformative changes across entire industries, opening up fresh prospects while also presenting risks for those who fail to keep pace. Embracing circular practices is becoming essential for businesses to thrive in this dynamic landscape.
Already in 2019, roughly 28% of professionals in supply chain functions disclosed that they have incorporated circular design processes in their company innovation strategy. And around 39% stated that they plan on implementing circularity methods within the next 2 years4.
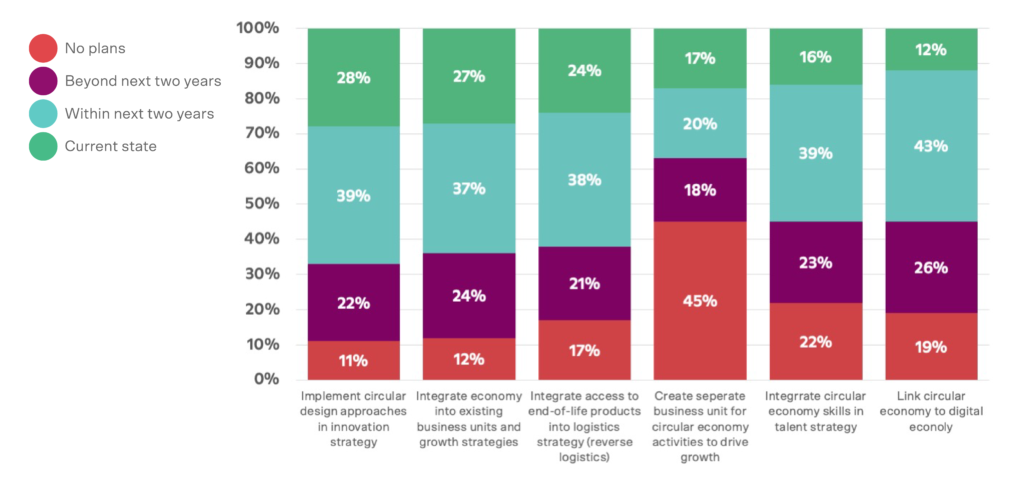
What Drives the Shift to Circularity?
Shifting consumer demand, regulation, technological progress, infrastructure, supply-side activity, and the macroeconomic environment are the main drivers of demand for circular consumer goods.
Shifting Consumer Demand
Research by McKinsey reveals that nearly 40% of European consumers consider sustainability to be of “high importance”. This heightened concern for sustainability is driving an increased demand for recycled, refurbished, and reused products. A recent survey conducted in 2021 indicates that approximately half of consumers in Germany, France, and the United Kingdom have already bought pre-owned items. As environmentally-conscious Generation Z individuals age, this trend is expected to gain further momentum3.
Regulation
Governments worldwide are progressively acknowledging the circular economy’s capacity to enhance competitiveness, foster robust supply chains, and achieve societal and environmental goals. Notably, the circular economy constitutes a fundamental element of the European Green Deal and features among the EU Taxonomy’s six environmental objectives. Several countries, including China, Chile, and France, have taken significant strides by implementing circular economy roadmaps and enacting legislation to promote sustainable practices. This growing recognition highlights the critical role of the circular economy in shaping future policies and fostering global sustainability5.
Other notable government initiatives are the Circular Economy Action Plan (CEAP) committing billions of euros to support initiatives that drive the journey towards achieving net-zero targets within the next decade. A central element of the CEAP involves a robust eco-design strategy, which emphasizes aspects like product longevity, reusability, upgrade potential, and advocating for a “right to repair.” Additionally, the plan emphasizes the integration of recycled materials, remanufacturing practices, and the promotion of high-quality recycling methods.
In the meantime, multiple European countries have begun the process of enacting extended producer responsibility measures. These initiatives offer substantial financial incentives to companies aiming to make the shift towards circular business models.
Technological Progress
Innovation progress in areas such as chemical recycling, digital product passports, and scalable disassembly technologies is allowing for the more and more accessible industrial-scale transition to circularity3.
The growing demand for solutions that facilitate product reselling, refurbishment, and recycling especially when it comes to developing scalable material collection and take-back programs, reverse logistics, as well as automated systems for material sorting, will drive further innovations in these areas, getting the industry a step closer to full circularity3.
Sources:
1 thredUP (GlobalData Market Sizing), ThredUP 2020 Resale Report,2020.
2 Bruna Alves, Circular material use rate in the European Union 2004-2021, https://www.statista.com/statistics/1316448/circular-material-use-rate-in-european-union/, June 2023.
3 Sebastian Gatzer, Stefan Helmcke, and Daniel Roos, Playing offense on circularity can net European consumer goods companies €500 billion, https://www.mckinsey.com/industries/consumer-packaged-goods/our-insights/playing-offense-on-circularity-can-net-european-consumer-goods-companies-500-billion-euros, June 2022.
4 Martin Placek, Supply chain approaches to the circular economy worldwide 2019, https://www.statista.com/statistics/1182874/circular-economy-supply-chain-approach/, April 2022.
5 Bocconi University, Ellen MacArthur Foundation, Intesa Sanpaolo (2021), The circular economy as a de-risking strategy and driver of superior risk-adjusted returns, http://www.ellenmacarthurfoundation.org/publications.
Resortecs policy asks Waste Framework Directive revision
1. Swift introduction of mandatory and harmonised Extended Producer Responsibility (EPR) schemes for textile products across the EU to introduce their separate collection.
2. Extended Producer Responsibility fees should be eco-modulated to incentivise producers to ecodesign their products. Design for disassembly must be included as a criterion.
3. Include a 2030 target for textiles-textiles recycling target as well as a fibre-to-fibre sub-target (for when the former is no longer an option to avoid premature downcycling). These targets should increase over time.
4. To deliver the waste hierarchy principles in practice, recognition and support of so-called pre-recycling techniques that are preconditions to effective circularity operations, such as sorting and disassembly, should be developed and integrated into the modernised Waste Framework Directive.
____________________________________________________________________
Action to make circular economy the norm is urgent. The Circularity Gap Report 2023 demonstrates that the world’s circularity has declined from 9.1% to 7.2% over the past five years, whilst total material extraction has almost doubled since 2000, reaching 100 billion tonnes today. As recognised by the EU Green Deal, the Circular Economy Action Plan, the EU Industrial Strategy, and the Textiles Ecosystem Transition Pathway, the textiles sector is key to the green transition as it is the fourth most resource intense industry, it accounts for 10% of global greenhouse gas emissions, and less than 1% of all textiles waste collected enters into a circular loop.
Resortecs supports the European Commission’s 2030 vision for a competitive, resilient, and innovative textiles sector laid out in the EU Strategy for Sustainable and Circular Textiles, particularly that all textile products placed on the EU market are eco-designed, sustainable and with producers taking responsibility for their products along the value chain with sufficient capacities for recycling and ending incineration and landfilling.
To achieve this ambitious vision, Europe must unlock industrial-scale circularity for textiles. Design for disassembly is key to unleash the full potential of textile-to-textile reuse, repair, and recycling. Even with an ideal circularity infrastructure, most textile products on the market would remain too complex or expensive to repair or recycle once they become waste because they are not designed for disassembly and, therefore, circularity. Once collected, most cannot be processed without a pre-recycling step such as disassembly. This is a key end-of-life-problem for the industry. For example, over 78% of all textile products are multi-material and the presence of zippers and trims like elastic bands hinder recycling. This results in material loss as most textile waste goes to incineration or landfill, and most new textiles products manufactured from scratch.
Disassembly is still a manual and costly process. To address this, Resortecs’ active disassembly innovations – a range of heat-dissolvable threads (‘Smart Stitch™’) and thermal disassembly system (‘Smart Disassembly™’) – helps to replace textiles designed for waste with textiles eco-designed for disassembly, thereby enabling material recovery for reuse, repair, upcycling, and high-quality recycling as well as waste prevention. Active Disassembly represents the pinnacle of Design for Disassembly methodologies (other pre-recycling available today include mechanical disassembly and manual disassembly). By incorporating releasable fasteners in a product’s design and assembly – such as Resortecs’ SmartStitch™ – active disassembly delivers an automatic, non-destructive, and economic industrial disassembly process that segregates components and materials of a product at its end-of-life.
A major benefit of Resortecs is that it acts as a drop-in solution to the textiles value chain as no significant infrastructure or manufacturing changes are needed in the value-chain for implementation of this technology. It also delivers circularity without compromising the creativity, design, and quality of clothing.
Click here or on the image below to download the full position paper.

Resortecs’ feedback on the call for evidence on Textiles Labelling Regulation revision
Resortecs welcomes the European Commission’s initiative to revise the Textiles Labelling Regulation. In addition to delivering on the targets set in the EU Strategy for Sustainable and Circular Textiles and the EU Circular Economy Action Plan, this revision is an opportunity to:
(1) Integrate information and labelling requirements on disassembly, alongside those that will be set under the Ecodesign for Sustainable Products Regulation (ESPR) delegated act on textiles and for the EU digital product passport (DPP).
(2) Boost the sector’s circularity by building a standardised information infrastructure that encompasses cradle-to-cradle, expanding from today’s cradle-to-gate/grave information infrastructure.
Today, the textiles industry heavily relies on a linear model and does not design products for circularity. Only 1% of all garments are effectively recycled. A main barrier is the complexity of disassembling garments. To recycle a garment, it first needs to be disassembled – currently this is still a manual, labour-intensive, and costly process. This means that without efficient disassembly at scale, there will never be a truly circular textiles ecosystem.
Resortecs’s active disassembly innovation provides the solution to make recycling easy. Resortecs’ system of heat-dissolvable threads and thermal disassembly is five times faster than traditional disassembly and makes it possible to recycle up to 90% of a textile product’s fabric content. It is also a drop-in solution to existing industrial processes.
To make smart disassembly the norm, Resortecs urges the European Commission to:
1. Set information and labelling requirements covering disassembly, ensuring consistency with the ESPR and the DPP.
2. Build a standardised information infrastructure that expands from today’s cradle-to-gate/grave to cradle-to-cradle, including information on disassembly. Making this information available is essential to enable value-retention operations such as disassembly and high-quality recycling and to recognise product materials and components that enable ecodesign, such as Resortecs innovative threads for textiles. An ecodesigned product will only fulfil its circularity potential if the information needed – including crucial information on how it can be efficiently disassembled – is readily available and accessible to the right actor. Such a standardised information infrastructure is not available today, meaning that consumers, sorters, recyclers, and manufacturers lack crucial information throughout, from making informative purchasing decisions to processing a garment once it reaches its end of life. A garment’s physical label should contain simple, harmonised, and comparable visual symbols reflecting its key circularity characteristics. A garment’s readiness for disassembly should be included to guarantee adequate sorting, processing, and waste prevention, as well as a garment’s recycled and recyclable content. This information should also appear in a textiles product’s DPP and provide the detailed information substantiating the physical label.
3. An ambitious Textiles Labelling Regulation that goes beyond its current strict focus on fiber identification is crucial to spur circular innovation and foster the development of novel fibers. It should grant recognition to emerging innovative novel fibers and set a regulatory framework that allows them to scale.
On 7 September 2023, Creamoda, EURATEX, Fedustria, and Resortecs welcomed 150 changemakers from 20 countries in Brussels to discuss the future of the fashion and textile industries.
Resortecs unveiled its latest report, “From Waste to Profit”– A Comparative Cost Analysis of Textile Disassembly Processes, available for download here, and highlighted the financial and operational benefits of Active Disassembly compared to the status quo disassembly methods – manual and mechanical.
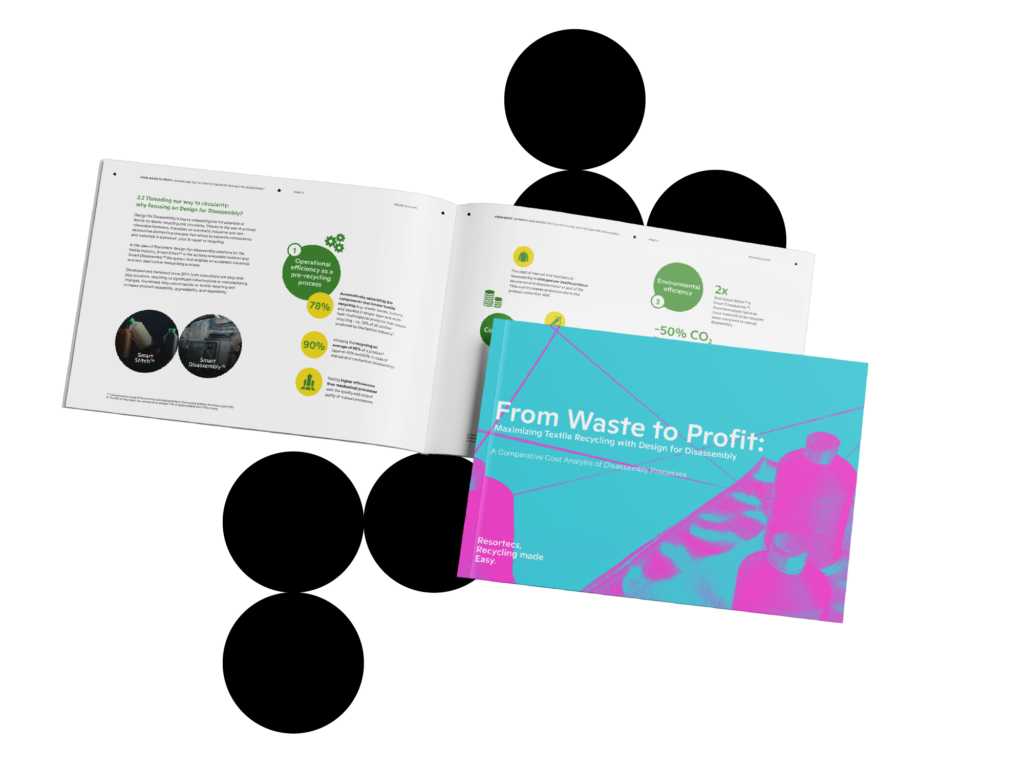
Dirk Vantyghem from Euratex gave an insightful update on the EU Textile Strategy launched last year with the aim to create a greener, more competitive textile sector. Textile products placed on the EU market need to be therefore more durable, repairable, recyclable, and to a great extent made of recycled fibers.
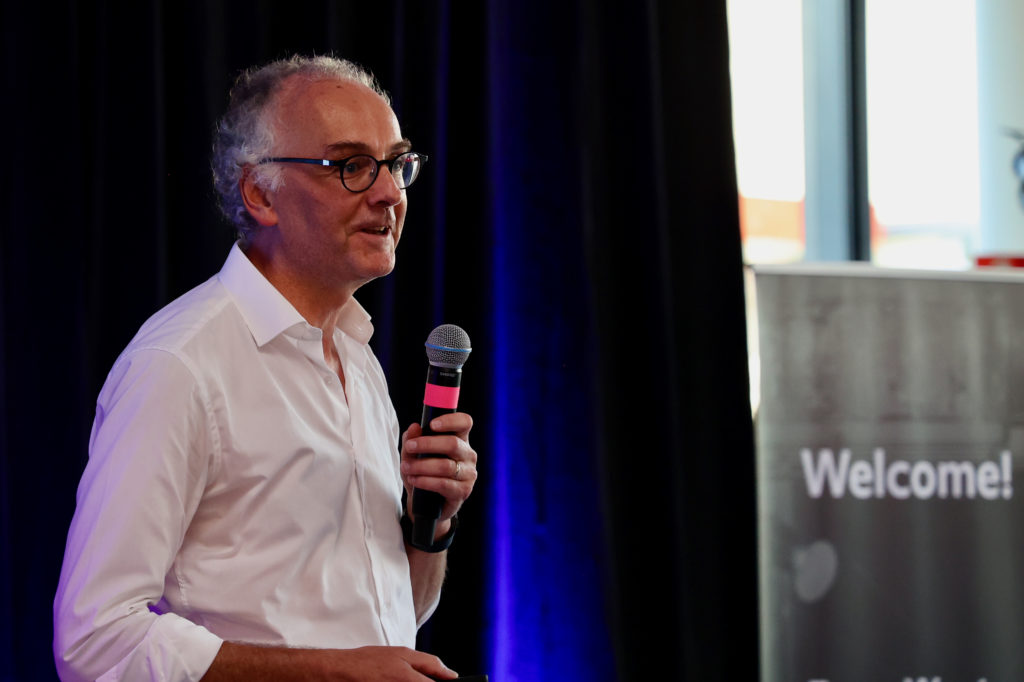
Textile recycling was highlighted as one of the solutions to drive change at scale and grow with environmental compliance, but getting there without losing the essential industrial competitiveness is of key importance for the sector.
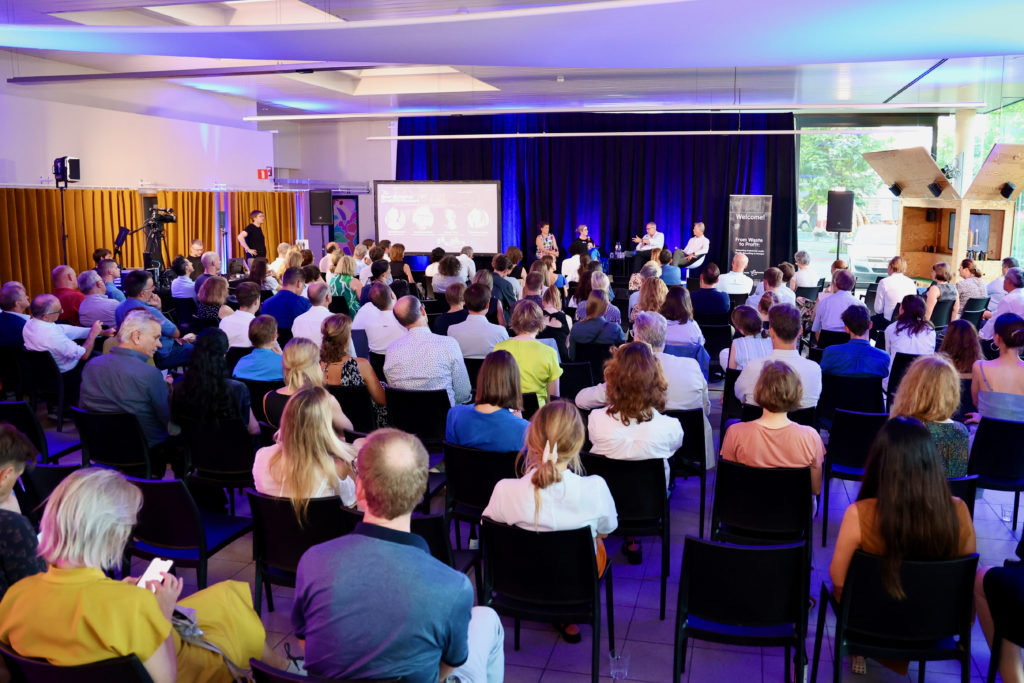
The panel discussions with Fedustria and industry leaders Concordia Textiles, Sioen, and BekaertDeslee – moderated by Christine Goulay from Sustainabelle, resulted in a number of interesting insights and testimonials on the efficiency and applicability of Active Disassembly for the textile sector.

Carl Baekelandt, Demet Tunc, Ivan Deceuninck, and Karla Basselier shared their expertise as circularity pioneers. Here are three takeaways from the insightful discussions:
1. There are now 16 legal changes focusing on the sustainability and circularity of fashion and textile companies rolling out across the EU — and more will follow.
2. 78% of all textile products require disassembly before textile-to-textile recycling.
3. Europe is becoming increasingly dependent on recycling textile waste due to 1) the shortage of raw materials and 2) the prohibition of recycled R-PET from the packaging industry for use in other sectors.
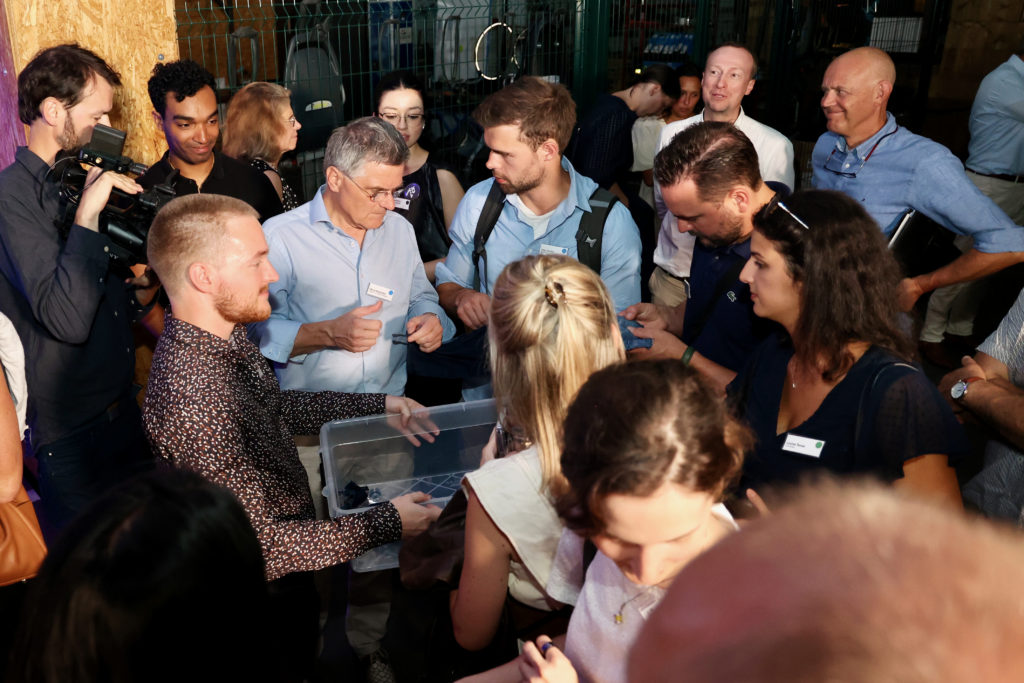
In addition, all guests also had the chance to explore Circularium and witness a live demo of Smart Stitch™ & Smart Disassembly™.
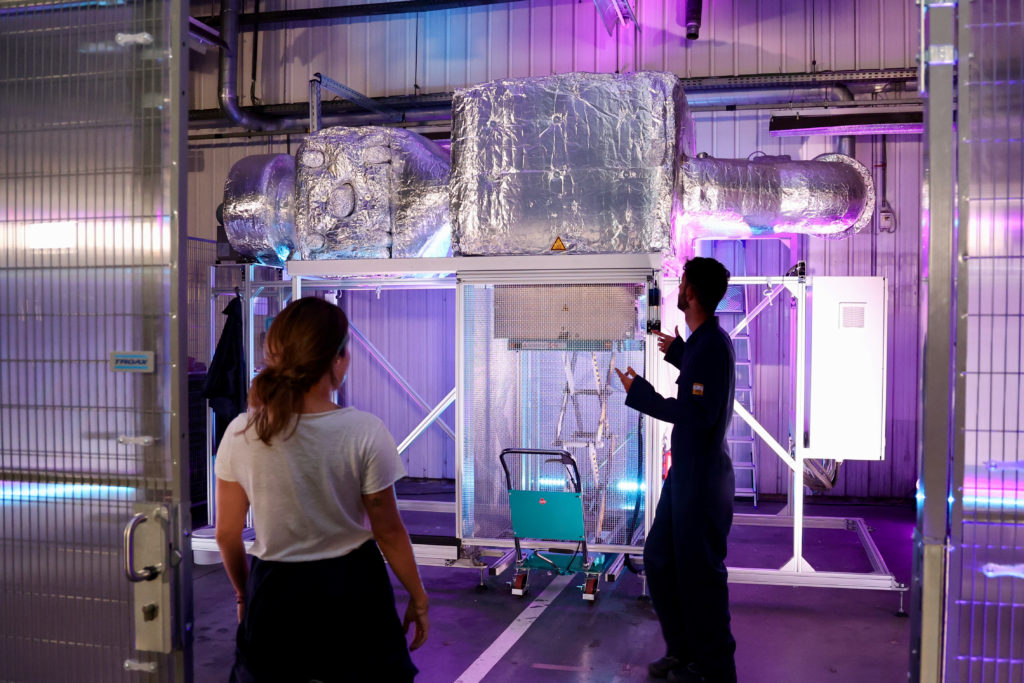
The need of collaboration to unlock industrial-scale recycling in Europe was eminent at the networking dinner & drinks at the end of the event. The connections made are testament to the commitment of all stakeholders along the textile value chain to make circularity a reality.
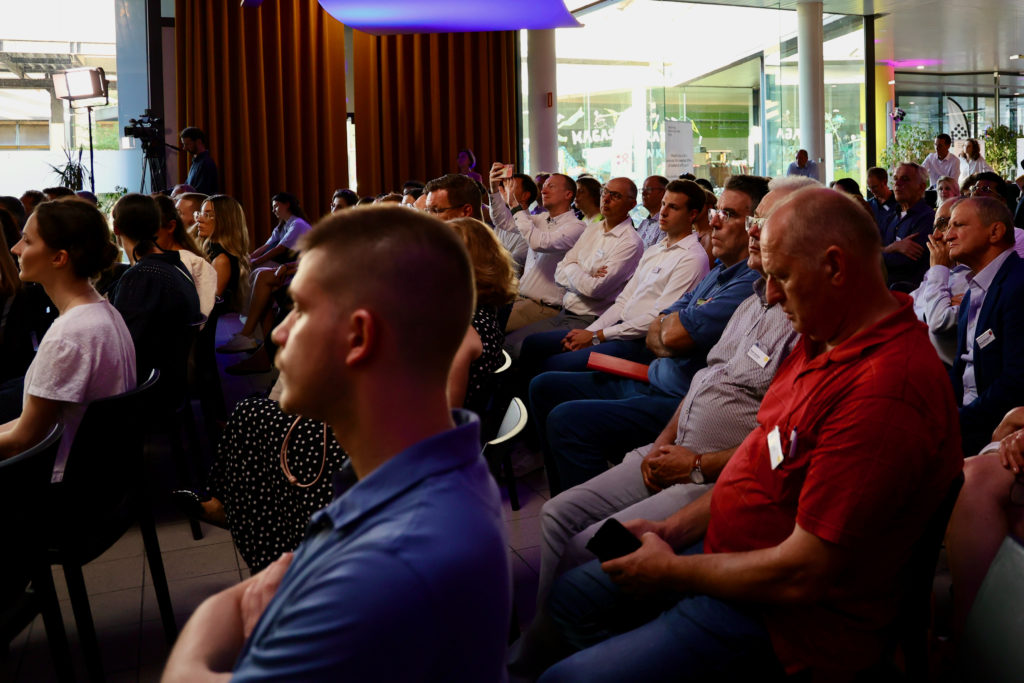
Have you already downloaded your free copy of the report ‘From Waste to Profit’ — A Comparative Cost Analysis of Disassembly Processes? Download it here.
What’s inside?
• The best-performing disassembly method for achieving maximum financial and operational efficiency.
• How different disassembly methods compare across four textile product categories: multilayer outdoor jackets, cotton trousers, aramid-based workwear, and mattress covers.
• How fashion and textile brands can transform product recycling into a source of ROI rather than costs at the end of a product’s lifecycle.
• What policymakers and brands should do to keep the European textile and fashion industries competitive.
Resortecs has partnered with BekaertDeslee, a global leader in the production of mattress textiles, covers, and modern sleep solutions. Together, both companies are taking Design for Disassembly beyond fashion to offer a groundbreaking solution for mattress cover recycling – reducing waste and increasing the recyclability of one of the most complex textiles products.
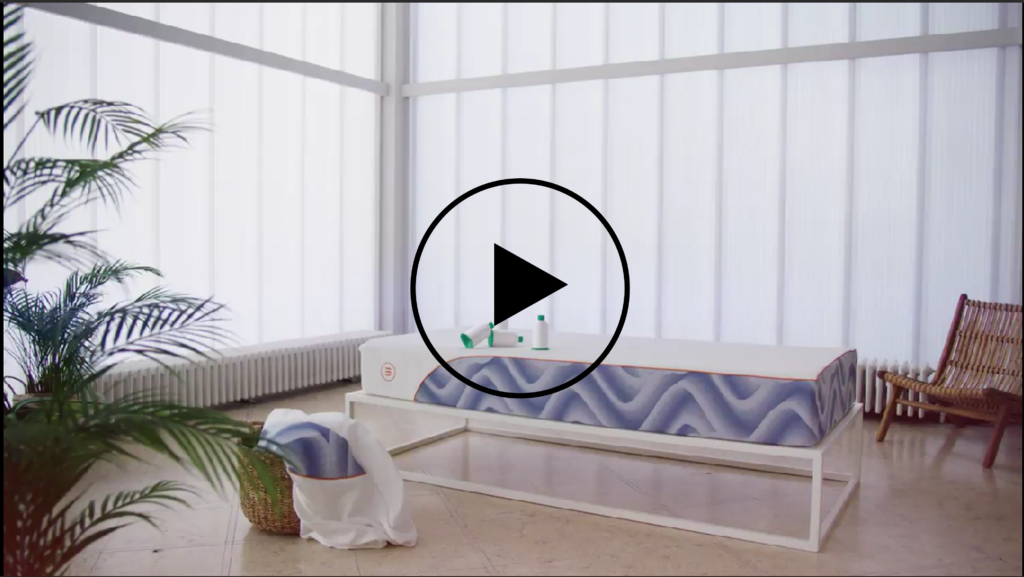
Currently, less than 1% of all textiles are effectively recycled. The remaining 99% end up landfilled or incinerated. The challenge of disassembling and sorting multi-material textile products is largely behind these staggering figures. In the case of mattresses, the textile cover is especially difficult to recycle due to its mixed materials and several components.
To tackle that, Resortecs and BeekaertDeslee have developed a unique and cost-efficient solution to make mattress covers that are made for being unmade. With the ultimate goal of easily dismantling, sorting, and recycling as much fabric as possible, BekaertDeslee will allow its clients to make mattresses using Resortecs’ Smart Stitch™ heat-dissolvable threads. The two companies have been working together since 2022 to create the first multi-material covers designed for industrial-scale disassembly and recycling.
At the end of the cover’s life, mattress brands will be able to use Resortecs’ low-emission Smart Disassembly™ systems for easy pre-recycling disassembly. This will help the industry to avoid polluting end-of-life processes (e.g. incineration), boost its recycling rates, and reduce each product’s carbon footprint.
As a circularity leader, Resortecs sees the partnership with BekaertDeslee as a significant step towards achieving industry-wide textile circularity. The two companies will continue to work together to develop innovative solutions that reduce waste, increase recyclability and promote a greener future for the industry and the planet.
Resortecs is one of the 13 winners of the Make it Circular Challenge!
On May 3, the 13 winners of the Make it Circular Challenge were announced. A total of 650 circular initiatives from over 20 different countries participated in the highly competitive challenge organized by the IKEA Foundation and What Design Can Do.
According to the challenge’s international jury, Smart Stitch™ and Smart Disassembly™ “represent the very best of design innovation and have the potential to make a significant impact in promoting sustainability and circularity.”
The Make it Circular Challenge
The competition was launched last year by WDCD and the IKEA Foundation to identify and support some of the world’s most promising circular innovations and enterprises. From hundreds of entries worldwide, 13 exciting visions for a restorative and regenerative future were selected, from seaweed packaging to waste-based textiles and upcycling marketplaces.
In addition to a €10.000 prize fund, the winners of the Make it Circular Challenge will have access to a six-month-long development program. The program was co-created by experts from the global Impact Hub network, providing the winning teams with the expert mentorship, guidance, and tools they need to grow their businesses and expand their impact on the world. The International Jury, consisting of 11 influential figures in circular design and entrepreneurship, including Bas van Abel (Fairphone), Corinne Gray (Unreasonable Group), Arthur Huang (Miniwiz), and Tamara Streefland (Built By Nature), was responsible for determining which of the 50 nominees had the most potential and would best benefit from this development program.
Selected by Secrid
Resortecs is also one of the three special projects to receive additional press and assistance. Secrid, a carbon neutral wallet producer, has chosen the 3 winning projects as part of their Impact Fund program, pledging to devote 1% of its revenue to bringing together designers and supporting their efforts to create products that enhance the planet’s natural and social equilibrium. By supporting Resortecs, Secrid aims to accelerate the development of the next generation of designers and promote change in our industries.
• Seed investment and EIC grant combined, the startup is tapping into €4.7M to boost production in 2023 and increase tenfold its disassembly capacity in 2024.
• Belgian Prime Minister, Alexander De Croo, highlighted the importance of funding circular entrepreneurship in a visit to the startup’s warehouse in Brussels.
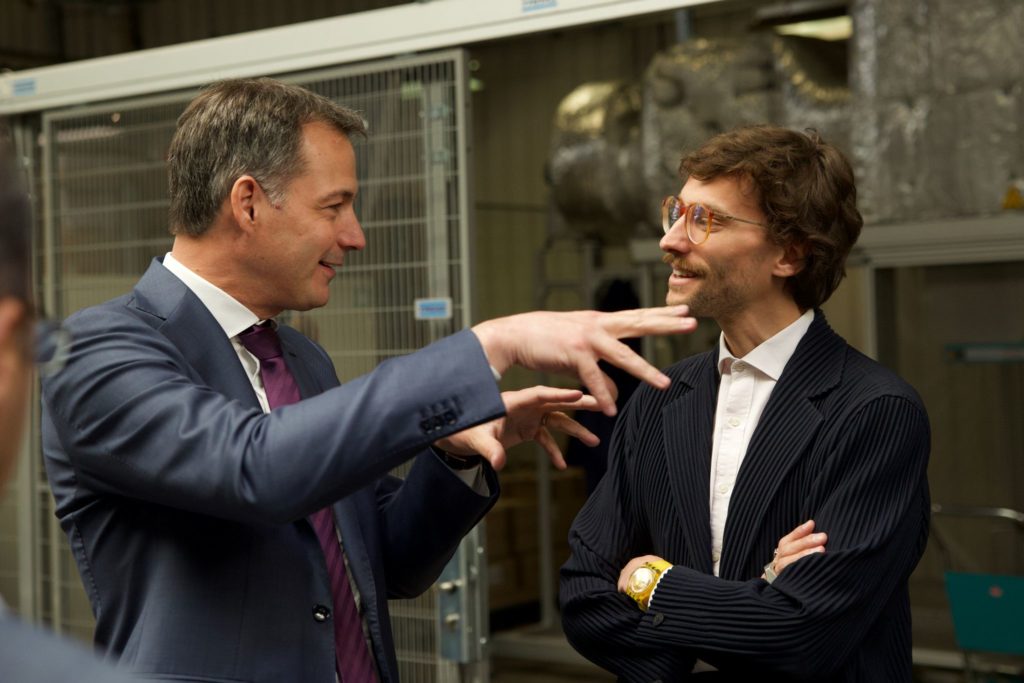
BRUSSELS, BELGIUM – 26 April, 2023 – Belgian startup Resortecs has raised €2.2 million in a seed investment round led by Brussels-based ScaleFund and finance&invest.brussels. Founded in 2017, the fashion tech company develops design-for-disassembly technology to make textile recycling fast, easy, and cost-efficient.
makesense_invest, AFI Ventures (the impact arm of Ventech), Trividend, and PDS Limited also joined the funding round, which follows a €2.5 million grant received from the European Innovation Council (EIC) in 2022. In total, Resortecs is tapping into €4.7 million to boost production this year and finalize the development of a continuous disassembly line, scaling up tenfold its pre-recycling processing capacity to 10T/day in 2024.
Currently, less than 1% of fashion’s production is recycled, meaning a yearly loss of materials worth €500 billion and placing the sector in the world’s top 5 polluting industries. Behind these figures is the complexity of sorting recyclable and non-recyclable materials.
With Smart Stitch™ (heat-dissolvable thread) and Smart Disassembly™ (industrial-scale thermal disassembly system), Resortecs enables brands to make textile products designed to be easily sorted and disassembled for recycling. Bershka, Decathlon, and H&M already use Resortecs’ Smart Stitch™ heat-dissolvable threads in products sold in over 60 countries.
“Our goal is to reduce the textile industry’s carbon footprint by 40 billion tonnes of CO2 by 2040. For that, we have to think big and take design for disassembly beyond fashion. Our headcount has doubled in less than 6 months. In just a few weeks, Smart Stitch™ will also be found on the world’s first mattress covers designed for disassembly, made in collaboration with Belgian sleep industry leader BekaertDeslee.” – explains Cédric Vanhoeck, Resortecs’ co-founder and CEO.
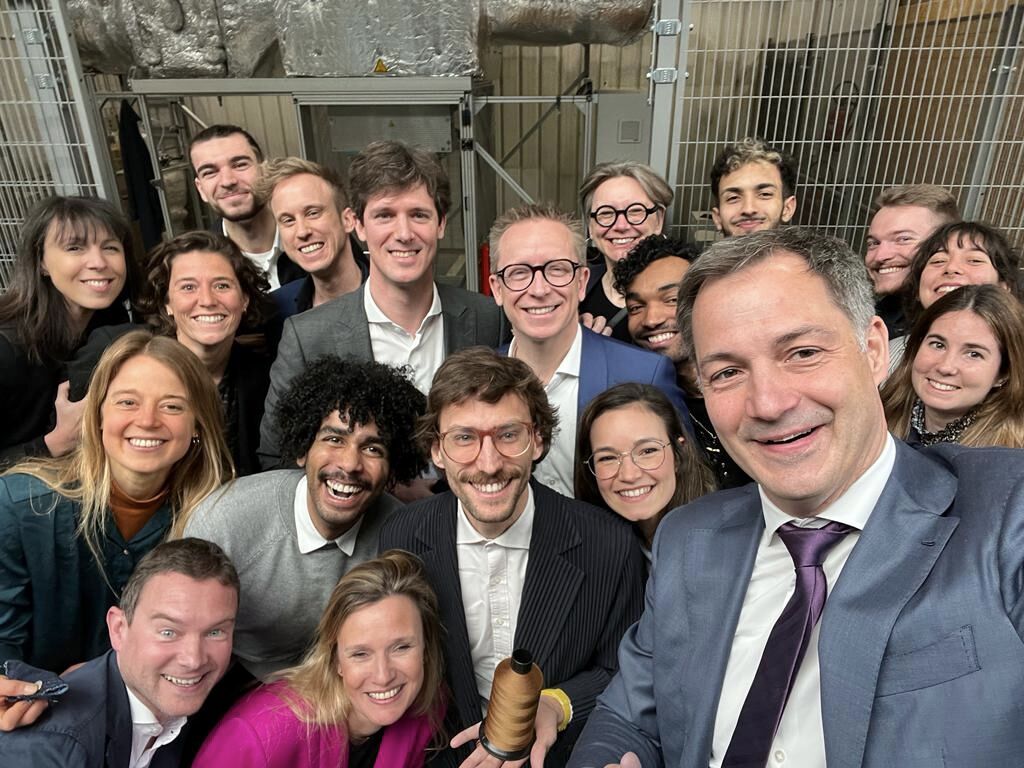
The Belgian Prime Minister, Alexander De Croo, visited the startup’s warehouse in Brussels on 26 April and highlighted the importance of investing in Belgian circular entrepreneurship:
“As Europe does not have many natural resources, we have to make a choice: we can either look at everything we have already produced as waste, or consider it as potential future raw materials to protect the planet. Innovations like this are key to strengthening our industrial competitiveness. Resortecs is a fine example of green growth and Belgian innovation that is ready to take the world!”
Join us.
Subscribe to our newsletter.
By subscribing, I agree with having my personal data stored and processed by Resortecs so I can receive future updates and marketing offers.
