Resortecs x Sioen: The start of a European consortium for workwear textile waste management
Resortecs, a leader in textile eco-design and end-of-life waste management, partners with Sioen, a global leader in technical textiles and protective clothing, to create workwear that combines durability with circularity. This collaboration is a major milestone in developing workwear that meets the highest safety standards while being designed for disassembly and recycling at the end of its lifecycle.
Under the agreement, Sioen will be integrating Resortecs’ Smart Stitch™ heat-dissolvable threads into its workwear production. This enables the creation of eco-designed garments that can be efficiently disassembled and recycled without compromising quality, comfort, nor protective functionality. Resortecs, on the other hand, will offer its comprehensive textile waste management service, that includes the disassembly and sorting of the discarded and returned textile products, as well as facilitating the recycling of the sorted textile materials.
Bart Vervaecke, CEO of Sioen’s Protective Clothing division, commented:
“Sioen together with Resortecs makes a big step in ready-to-dismantle garments with this cooperation. We are proud that with our support we can enable Resortecs to install their EU-based disassembly line. Resortecs’ technology will play an important role as a fully integrated part of our sustainable strategy at Sioen, drastically improving the end of life solution for our garments.”
The beginning of a textile waste management circularity consortium in Europe
This collaboration lays the foundations of a Resortecs-led consortium in the Benelux and France regions for end-of-life textile waste management of workwear. The consortium will unite the efforts of workwear manufacturers, recyclers, government agencies, and Resortecs, to facilitate an operationally optimised and financially viable circular textile waste-management solution for complex apparel.
At the heart of the consortium is a Smart Disassembly™ line, with an annual processing capacity of 3000 tons, that will be placed and operated in Belgium by Resortecs by the end of 2025. The Smart Disassembly™ pre-processing line will integrate with existing sorting and collection infrastructure, as well as current and upcoming recycling technologies.
Resortecs’s holistic waste management solution uses an innovative technology to solve a critical challenge in textile recycling. By automatically eliminating trims that block recycling and reclaiming double the amount of a product’s textile content, up to 15x faster, Resortecs facilitates circularity on an industrial scale. As a result, high-performance workwear, along with other textile products like mattress covers and fashion garments, can now be disassembled and recycled more effectively.
Workwear manufacturers operating in Belgium, Netherlands, Luxembourg and/or France can now take part in the consortium by simply producing their textile products with the heat-dissolvable Smart Stitch™ sewing threads. Once those textile products have reached their end-of-life, they are delivered to Resortecs for disassembly, sorting, and recycling. Get in touch to learn more.
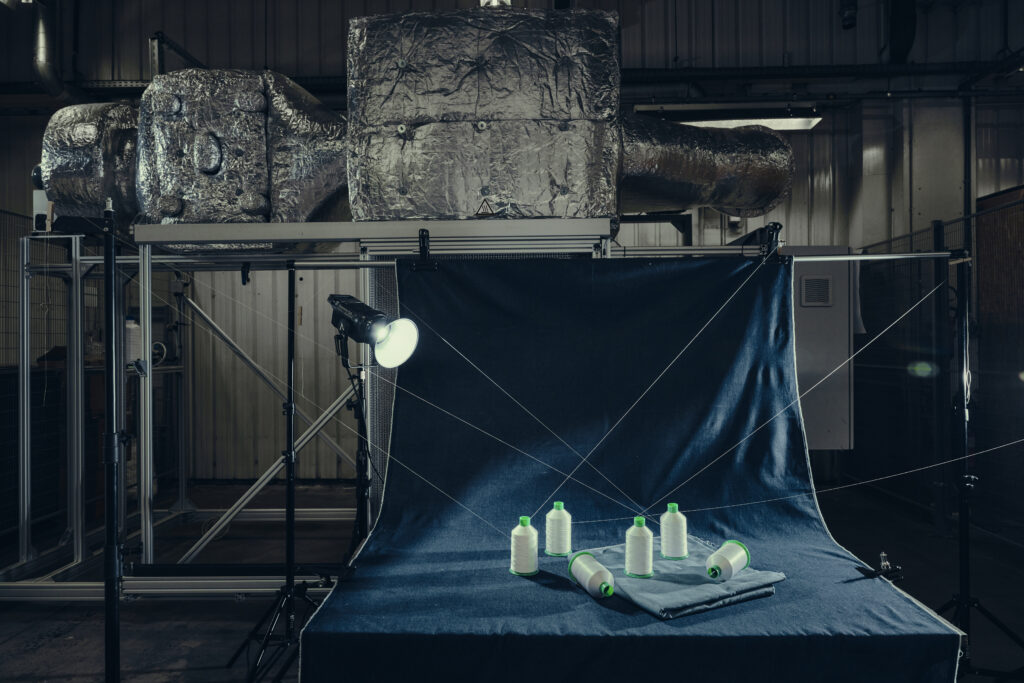
A new circular standard for protective textiles
This collaboration marks a crucial step towards setting circularity as the new standard in the protective clothing and technical textiles sectors, with the goal of producing over half a million of fully recyclable garments with Sioen in the coming 3 years.
Cédric Vanhoeck, CEO and co-founder of Resortecs, commented:
“As we drive circularity in protective textiles, we’re challenging industry norms. Many believe that circular design can’t align with safety standards, but we’re proving otherwise.This collaboration shows how innovation is key in the sector for building a more sustainable future without technical compromises.”
By combining Sioen’s expertise in protective gear with Resortecs’ cutting-edge Design-for-Disassembly technology, the partnership is setting a precedent for workwear that protects both workers and the environment.
“It’s galvanising to see one of the biggest workwear players in Europe supporting our efforts in creating a pan-European network of disassembly and pre-processing infrastructure. We are actively looking for other market leaders in other European regions such as DACH, Iberian Peninsula, and Scandinavia with whom we share the same vision in rejuvenating the European textile industry”, added Cédric Vanhoeck.
About Resortecs
Resortecs® offers pre- and post-consumer textile waste management services for the fashion, workwear, bedding and automotive industry. The company offers heat-dissolvable stitching threads (Smart Stitch™) and thermal disassembly systems (Smart Disassembly™) that enable easy, automated textile recycling on an industrial scale. Resortecs’ mission is to lead the textile industry towards full circularity by facilitating Design-for-Disassembly (DFD).
About Sioen
Sioen is a global leader in technical textiles, colouring solutions and protective clothing, providing high-performance solutions for a wide range of industries, including workwear, firefighting, military, and forestry. Dedicated to innovation, Sioen combines advanced materials and cutting-edge designs to ensure maximum safety and durability, all while striving to promote sustainability through the development of circular products.
More information about Sioen can be found online at: https://sioen.com/en
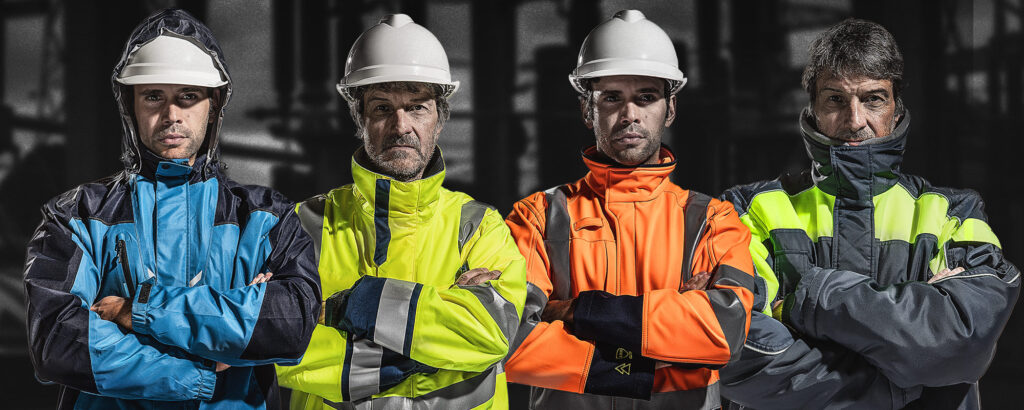
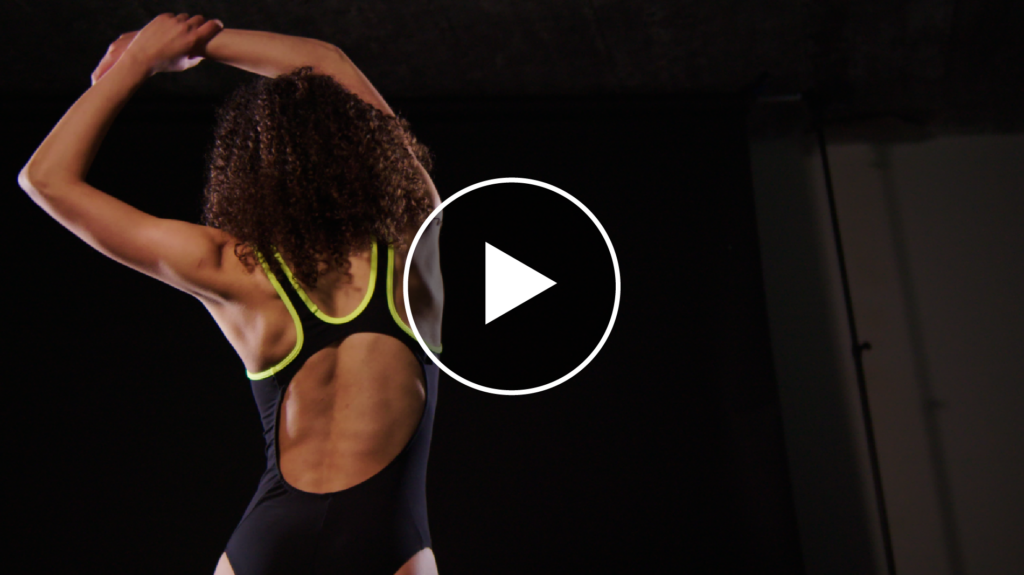
Resortecs has joined forces with Decathlon, the global leader in sports equipment and apparel, to develop a fully recyclable swimwear collection without compromising performance, functionality, or aesthetics. This collaboration blends state-of-the-art technology with high-performance design.
Acerina Trejo Machin, the Chief Technology Officer at Resortecs, explains, “We all know that a high percentage of elastane prohibits the recycling of fabrics, but eliminating elastane lowers the functionality and performance of a garment. To balance performance and recyclability, Decathlon developed Negombo, a fabric ensuring elasticity without the use of elastane.”
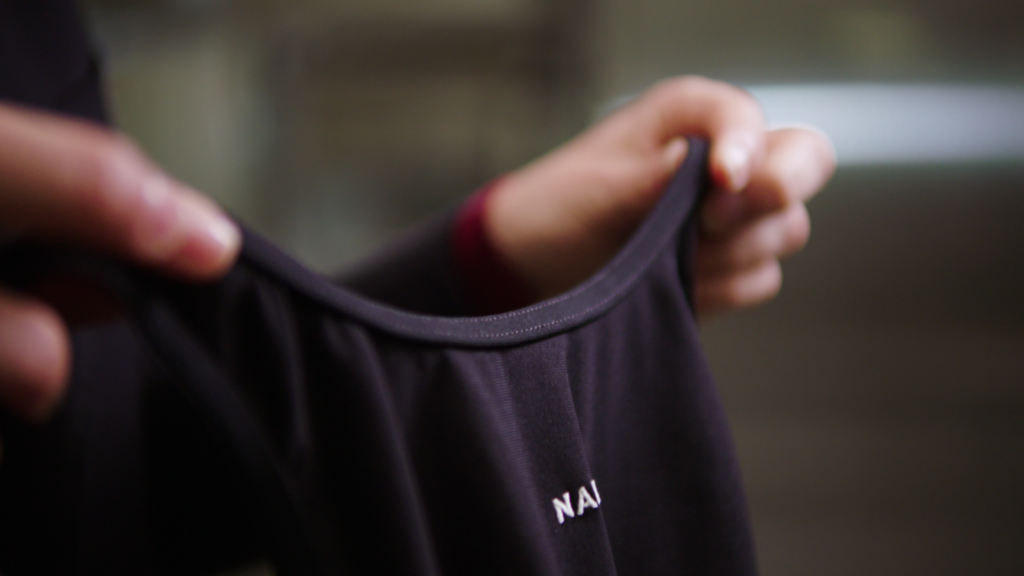
However, creating a swimwear garment with a recyclable fabric alone isn’t enough to meet the required performance and comfort, for which elastic bands are needed. Those elastic bands are not processable by recyclers and block the recycling of the swimwear. This is where Resortecs comes into play. Resortecs’ Smart Stitch™, combined with Smart Disassembly™, enables the efficient separation of the elastic bands from the main fabric at the end of the garment’s life cycle.
Acerina elaborates, “Resortecs’ active disassembly process ensures the maximum recyclability rate of the swimwear garment. Our technology allows for fully automatic disassembly, without any manual intervention, at a scale of up to 10 tons a day. This results in an impressive 63% increase in material recovery and is 10 times faster than conventional methods.”
The synergy between Resortecs and Decathlon allows for the creation of swimwear that is not only high-performing but also fully recyclable, without making any compromises in design, durability, or comfort.
Closing the loop has never been easier. By incorporating Resortecs’ disassembly solution, product designers can ensure circularity while focusing on their ultimate goal: creating garments that best fit their customer needs.
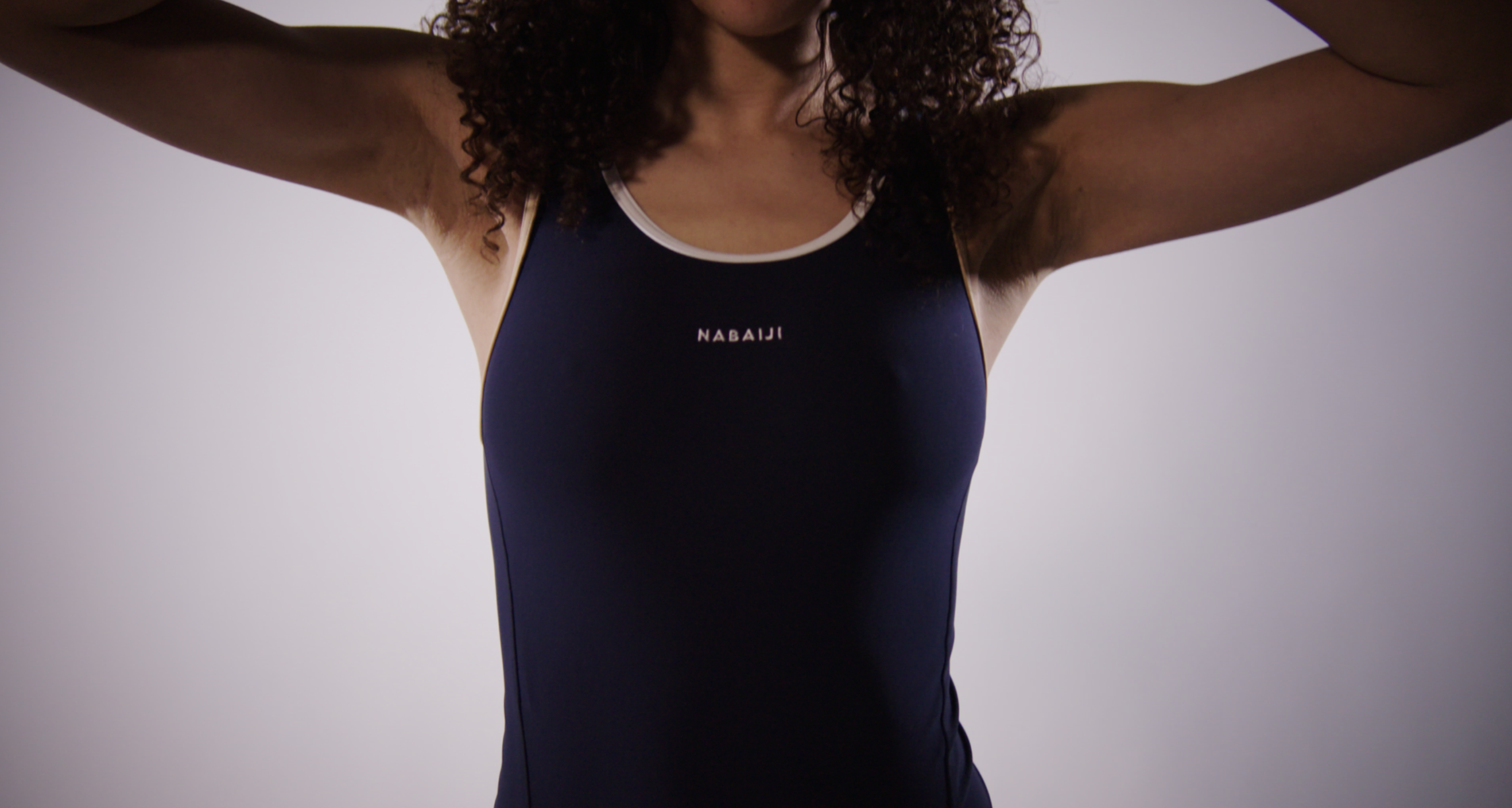
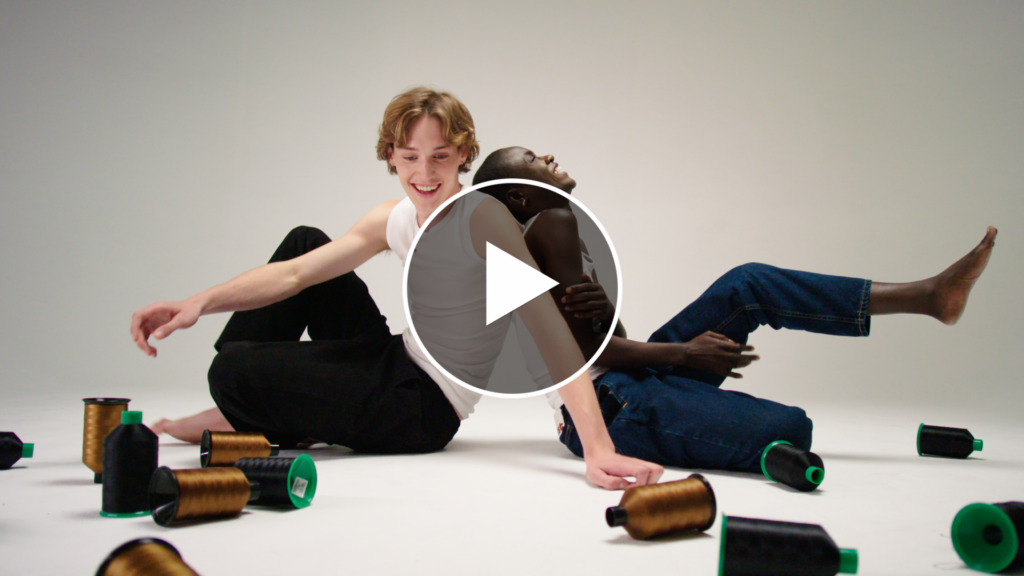
HNST Studio, the Antwerp-based label dedicated to creating jeans that embody transparency and circularity, partners with Belgian eco-design innovator Resortecs to launch new products made to be unmade—easy to disassemble for repair and recycling at the end of life.
The partnership debuts with the newly introduced Geri (for women) and Simon (for men) pants: crafted with up to 70% recycled cotton, these are HNST’s first jeans to feature an elastic waistband and drawstrings for unparalleled day-to-day comfort and flexibility.
Completely eco-designed for recycling, the jeans’ waistbands are stitched using Resortecs’ Smart Stitch™, an award-winning thread engineered to disappear under heat. This thread change at the design phase ensures that the jeans can be disassembled without manual intervention at the end of their lifecycle—allowing for their recyclable fabric to be automatically sorted out of the non-recyclable materials added to the waistband for more comfort.
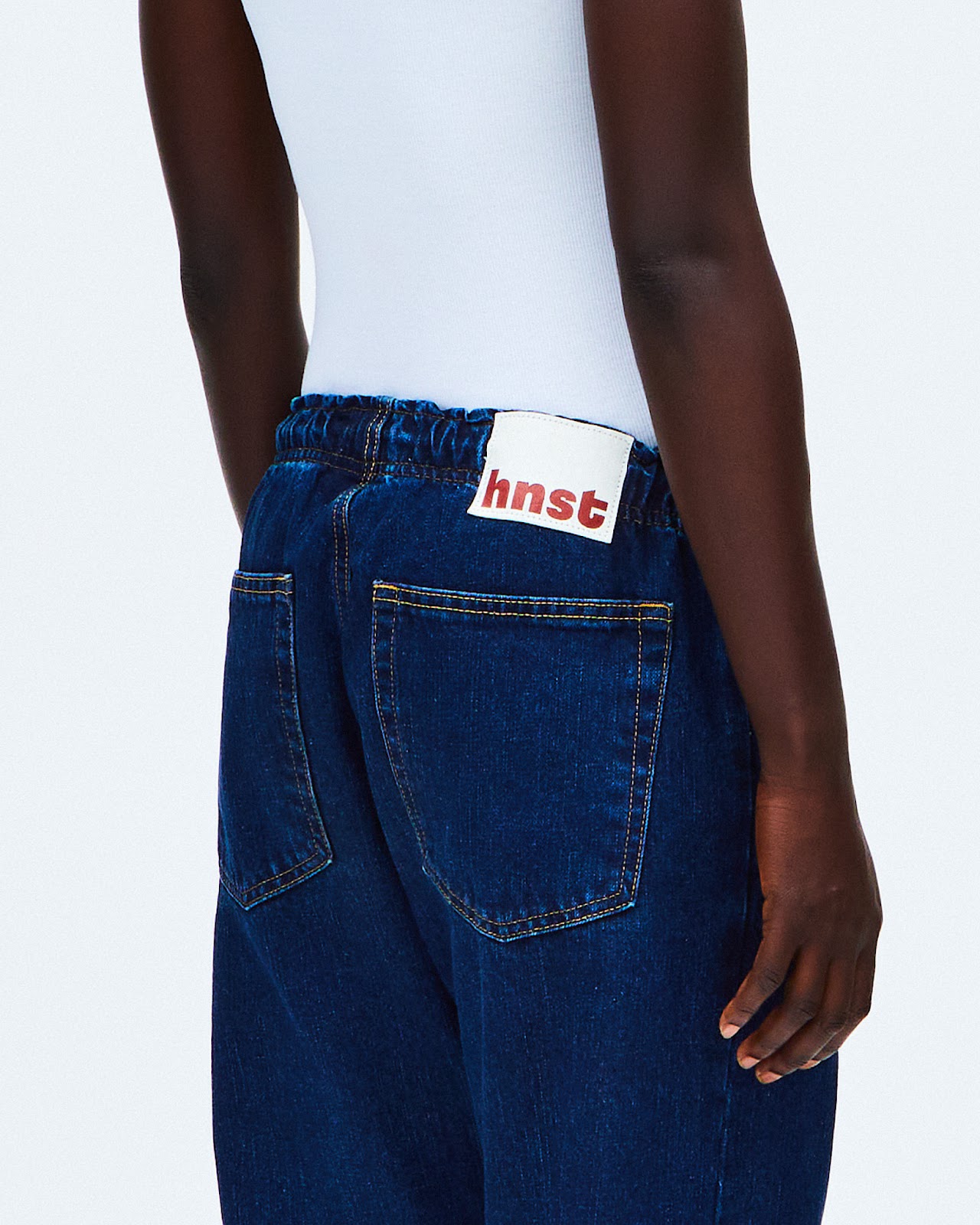
“Our other jeans didn’t have elastic waistbands because they would be critical blockers for recycling. Collaborating with Resortecs allowed us to explore new possibilities to give our customers more comfort without compromising our non-negotiable commitment to circularity” stated Eva Engelen, Sustainability and Product Manager at HNST.
“We are two Belgian innovators trying to rewrite the future of fashion in a circular way,” said Cédric Vanhoeck, CEO at Resortecs. “This partnership with HNST showcases how our technology can unlock new possibilities for fashion players that want to design for recycling while keeping the creativity, functionality, and quality of their products”, he added.
The Simon and Geri pants are just the first drop of the HNST x Resortecs partnership. Both companies are committed to further integrating Resortecs’ design-for-disassembly solutions into other HNST designs, solidifying their shared vision of establishing circularity as the standard in the fashion industry. Consumers everywhere can now shop the collection at letsbehonest.eu and at select independent retailers in Europe, North America, and Japan.
BRUSSELS, BELGIUM – Wedze, the winter-sports brand of French giant Decathlon, partnered with Belgian innovator Resortecs to launch a fully recyclable ski jacket using the start-up’s design-for-disassembly technology.
Different from normal ski jackets, which are extremely difficult to recycle due to their complex material composition, this flagship is made of 63% recycled polyester, and 23% of the fabrics are dyed using dope dyeing – one of the most water-efficient dying techniques.
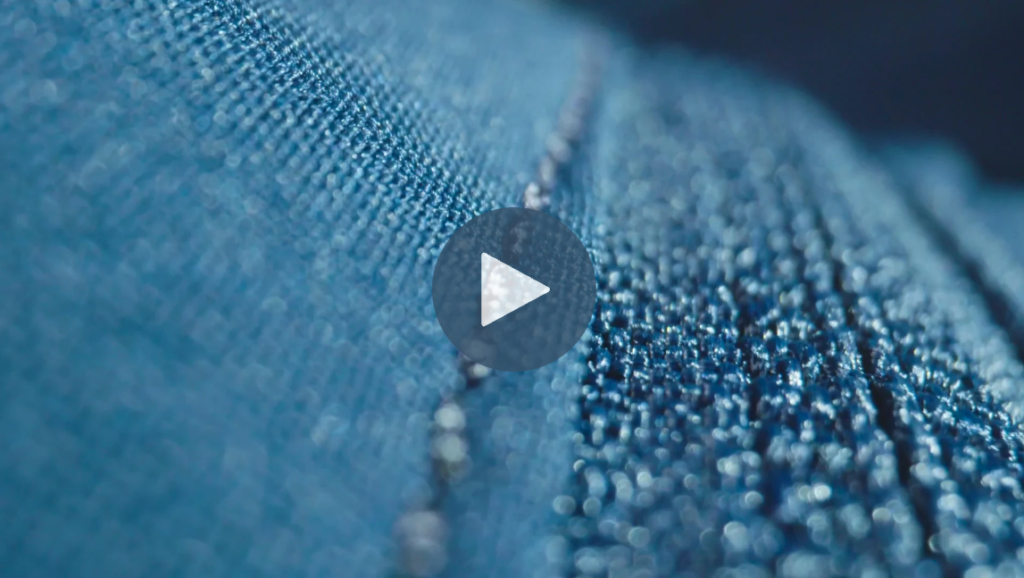
As making a completely mono-material jacket isn’t yet possible , Wedze found in Resortecs the ideal partner to bring its first fully recyclable ski jacket to life. The start-up’s Smart Stitch™ threads melt and disappear when exposed to temperatures above 190°C, ensuring that the non-recyclable zippers, press buttons and elastics bands can be easily separated from the polyester parts when it is time for recycling.
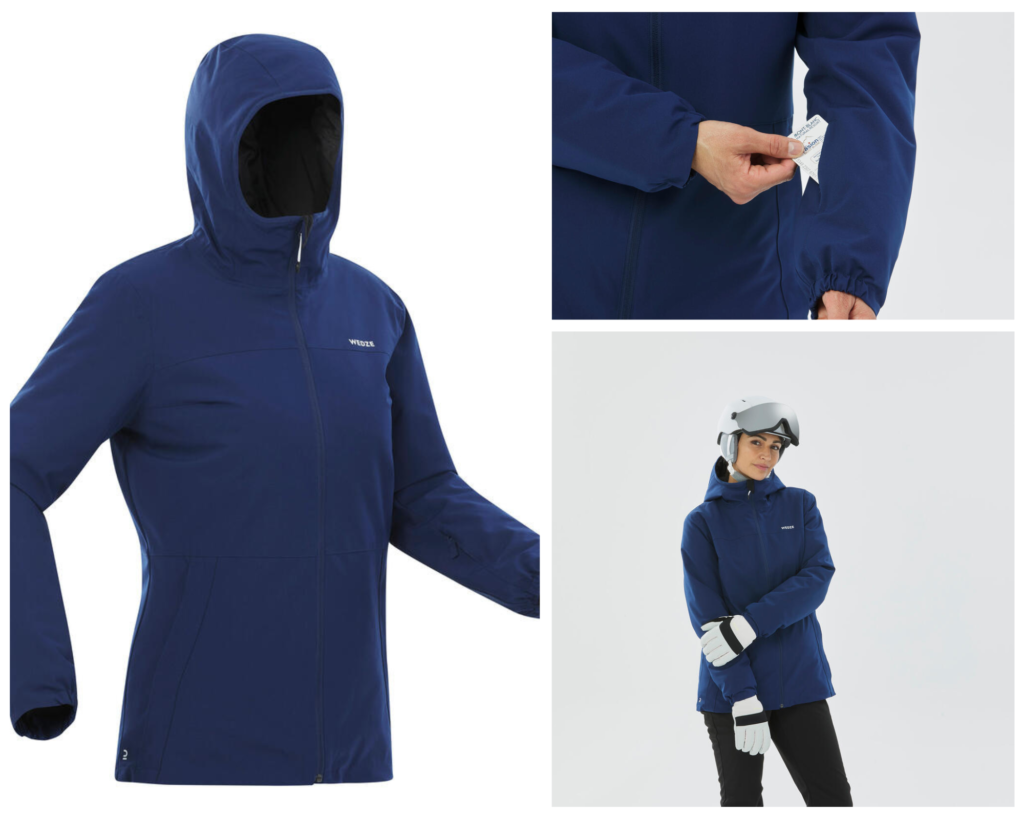
“Clients who want to join our circularity efforts can return their used jackets when they are no longer fit for use, and we’ll recycle them into new products.” Explains Fern S., Product Engineer and Sustainable Development Leader at Wedze.
“We are excited to launch a product with Wedze because, like the entire Decathlon group, they are known for their efforts to develop more sustainable products. The jacket looks great and has infinite possibilities for its next lifecycle.” – Cédric Vanhoeck, co-founder & CEO at Resortecs
Decathlon joins H&M and Bershka (Inditex Group) in our client roster and becomes the 3rd major global brand to launch products with Smart Stitch™ and Smart Disassembly™ in less than a year.
Skiers who don’t want to compromise on sustainability when hitting the slopes can find the disruptive jacket at Decathlon stores in Spain and online at www.decathlon.com for all other European markets.
Resortecs – REcycling, SORting, TEChnologieS – is an award-winning start-up that develops design-for-disassembly solutions. We drive full circularity in fashion with heat-dissolvable stitching threads and thermal disassembly systems that make recycling easy.
For further inquiries:
Davidson Leite
Communications & Branding Lead
[email protected]
BRUSSELS, BELGIUM – Brussels-based start-up Resortecs is partnering with Bershka, a global fashion brand part of the Inditex Group, to launch a new capsule collection using the start-up’s design-for-disassembly technology to facilitate recycling and upcycling.
The collaboration brings together summer and circularity in two unisex products – denim shorts and jeans – made with Resortecs’ Smart Stitch™ for easy disassembly. The products will be available online and at selected stores in 60 markets across the world as of 5 August.
Resortecs aims to boost textile recycling with two patented innovations: Smart Stitch™, heat-dissolvable stitching threads, and Smart Disassembly™, an industrial oven capable of taking apart the different components of clothing made with Smart Stitch™. This way, the start-up expects to reduce the high costs and complexity of separating different textile materials ahead of recycling.
For Bershka, this collaboration is part of Inditex’s Sustainability Innovation Hub: an open-innovation platform that works alongside start-ups, academic institutions, and tech centers to promote and scale disruptive solutions for new materials, technologies and processes that reduce the environmental footprint of fashion products and help advance towards circularity.
Founded in 2017 by Cédric Vanhoeck and Vanessa Counaert, Resortecs has already validated its solution with over 30 international fashion players:
We are thrilled to work with Bershka. Since day one, we’ve been positively
surprised by how much their team is committed to the circular transition.
The final products look great and have infinite possibilities for their next
lifecycle. – Cédric Vanhoeck, co-founder & Executive Lead
Resortecs – REcycling, SORting, TEChnologieS – is an award-winning start-up that develops design-for-disassembly solutions. We drive full circularity in fashion with heat-dissolvable stitching threads and thermal disassembly systems that make recycling easy.
For further inquiries:
Davidson Leite
Communications & Branding Lead
[email protected] | +32 0494 94 93 54
What an incredible closure to Resortecs’ participation in Desigual + Plug and Play Tech Center’s Awesome Lab – Spain’s first fashion-tech acceleration program!
This acceleration program supports selected startups through mentorships, training, providing resources and tools, and funding. This initiative aims to boost the development of technology solutions that will face the main challenges of the fashion industry.
Resortecs was chosen for its technological solution and innovation at the service of the circular economy. The challenge proposed by the Awesome Lab was to assign a new use to garments to give them a second life. Resortecs worked alongside Desigual for 8 months on a pilot where the Spanish giant implemented Resortecs’ technology in a strategic manner in order to build together the future of fashion.
Last week, Resortecs was invited to the Awesome Lab’s final Demo Day in Barcelona to pitch the results of the collaboration. But Resortecs didn’t stop there. Not only did our team give a great pitch, but they also won the award for “best project presentation”. Indeed, the collaboration showcased successful results and optimistic insights on collaborations between technologies such as Resortecs and fashion brands, and on the future of circular fashion!
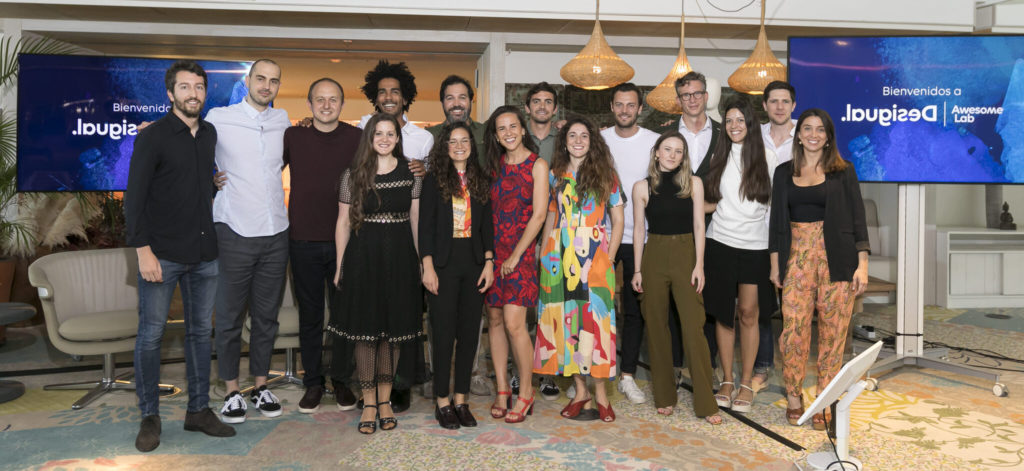
Resortecs is thankful for the incredible journey alongside Personify XP, Vestico, Syrup Tech, Exonode, Swearit, Shelly Xu Design, and looks forward to years of partnership for circularity con la marca más chula de la moda española!
Resortecs’ innovation – the first of its kind – can process up to 1 ton of garments per day and is being tested by 30 major global fashion brands
Recently, images of the mountains of unsold clothing dumped in the Atacama Desert, in Chile, shocked the world. Each year, 34 million tonnes of textiles worth more than 400 billion euros are wasted by the fashion industry – which became a strategic target of the EU Green Deal. Behind these alarming figures are the costs and complexity of disassembly and recycling. When faced with stacks of unsold inventory, that might reach up to 40% of each season’s production, fashion brands turn to options easier and cheaper than recycling, such as landfills or incineration. If it’s up to Resortecs, however, this scenario is about to change.
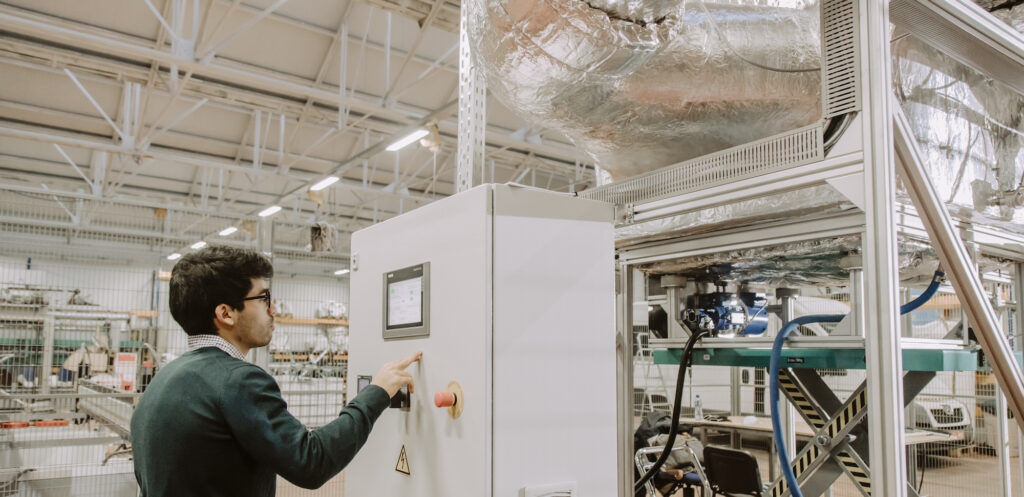
The start-up presents its first thermal disassembly system in a demonstration event for the press, politicians, investors, and industry peers in Brussels on Thursday, 09/12. The system combines heat and mechanical force to disassemble clothes stitched with Resortecs’ heat-dissolvable threads. Inside the system – a globally-patented, high-tech version of an industrial oven – the clothes are exposed to specific temperatures, making the seams disappear automatically and allowing for easy material sorting and recycling.
“The system works with little to no oxygen inside. This preserves the fabrics’ quality and prevents the clothes from burning, even when they are submitted to temperatures higher than 200° C”, explains William Allouche, Technical Lead for Disassembly and the mind behind the system’s engineering. “We’ve made sure to develop a closed-loop system to preserve the heat produced for each batch of clothes for the longest time possible. This ensures energy recovery and generates way less CO2 emissions than other heat-induced processes.”
The thermal process is 5x faster than traditional disassembly methods and enables the recycling of up to 90% of the original fabric material, instead of the usual 48% obtained after manual or mechanical disassembly. Using data to prove the impact of its innovation, Resortecs ran an externally-reviewed life-cycle assessment which shows that the process adoption could help the fashion industry cut its CO2 emissions by 50% and reduce waste generation by 80%. If the entire EU production were thermally disassembled and recycled, the fashion industry could generate 60.3 million fewer tons of CO2 and save up to € 2.3 billion per year.
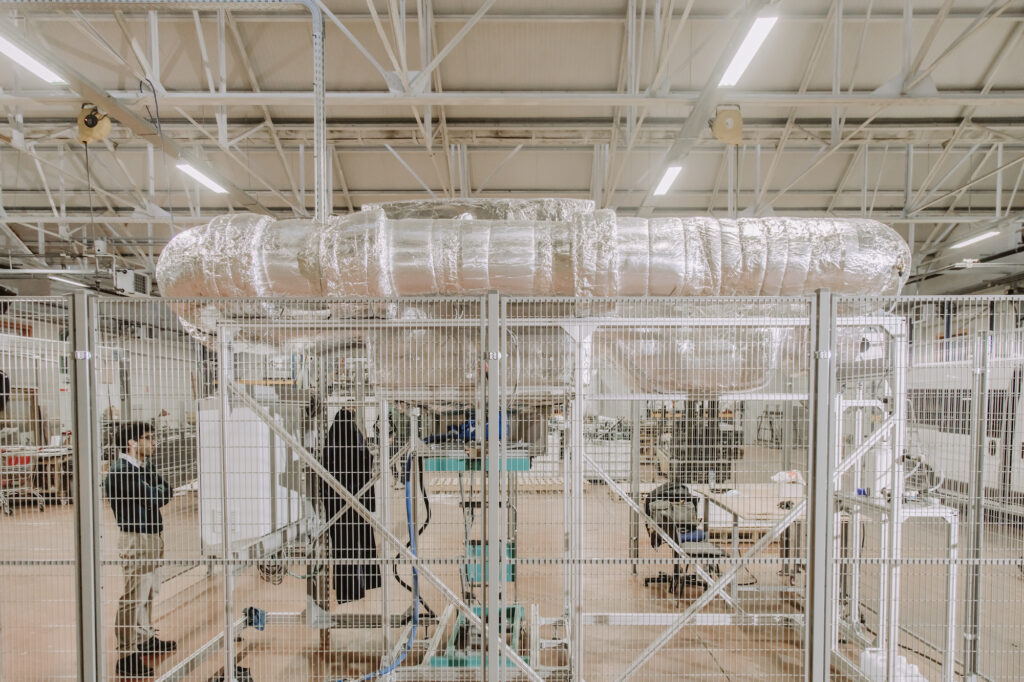
The version presented to the public is just a prototype. It can process up to 1 ton of textile per day and is being used to show first partners, such as the fast-fashion giant H&M and other 30 global fashion brands, how the start-up’s solution works. In the long term, it will be part of a network of thermal disassembly systems placed in recycling plants all over the world. The idea is to cover the globe with automatic thermal disassembly to speed up global textile recycling. Still in 2022, a second system with a larger processing capacity will come into operation. Together, both units will be able to prepare up to 13 tonnes/day of clothing for recycling, an unprecedented volume in the world.
“Everyone thinks of recycling, but no one looks at the biggest challenge to make it happen: disassembly. We saw an opportunity to optimize production while boosting up recyclability and sustainability, and we jumped on it” says founder Cédric Vanhoeck. “Brands have finally realized that there’s no way to continue producing and wasting textile as if nothing is happening with the planet. When we started 4 years ago, brands complained about the costs of sustainability, now they come to us because they understand that circularity is an investment.”
Join us.
Subscribe to our newsletter.
By subscribing, I agree with having my personal data stored and processed by Resortecs so I can receive future updates and marketing offers.
