Embracing Eco Design: How Modular Garments and Accessories Lead to a Circular Economy
Garments and accessories are often complex composites, made from various materials to meet distinct requirements. For example, shoes consist of a rubber sole paired with an upper made of leather or fabric. Tailor-made suits feature horsehair reinforcements in the front and lapel, combining wool exteriors with silk, viscose, or nylon linings. Winter jackets are filled with feathers, sandwiched between water-repellent fabric and synthetic linings.
For end-of-life treatments, these composite products present challenges. Each material requires a unique recycling process. To maintain the quality of recycled materials, components like the rubber sole of a shoe must be separated from the leather or fabric upper. This principle applies to all composite garments. Each material must be separated to ensure it can be reused in its pure, high-quality form.
Unfortunately, most apparel is not designed for easy disassembly. Disassembling different materials currently requires a labor-intensive and manual process. Consequently, “recycled” garments and accessories are often shredded into a low-quality textile mixture. Effective recycling and repair are virtually nonexistent.
To truly implement a circular economy and protect our future prosperity, we must consider product structures and hierarchy. Effective repair, remanufacturing, and recycling demand that garments and accessories be modular. Achieving this necessary modularity involves using reversible joining methods and prioritizing design for disassembly.
Resortecs is at the forefront of this revolution, providing design-for-disassembly solutions that enable high-quality textile recycling on an industrial scale. By pioneering innovative threads and disassembly techniques, Resortecs empowers brands, sorters, and recyclers to address today’s environmental challenges at the pace and scale the Earth needs.
Resortecs combines thermal engineering, eco-design, and chemical engineering to offer state-of-the-art solutions that empower the entire textile value chain to close the loop. Discover Smart Stitch™ and Smart Disassembly™: Resortecs’ solution for multi-material disassembly in a fast, easy, and cost-efficient manner. To learn more about the financial impact of design for disassembly, dive into the From Waste to Profit report.
Smart Stitch™ is a range of 16 heat-dissolvable threads – enabling automatic thermal disassembly and design for recycling. Suitable for a variety of applications, from apparel to fire-resistant workwear, the Smart Stitch™ threads have been exhaustively tested on various production line configurations and are compatible with every stitching machine widely available on the market.
Smart Disassembly™ is the world’s first thermal disassembly system – combining the quality of manual methods with the speed of mechanical processes. A fully automatic process empowering sorters and recyclers to disassemble textile products while removing zippers, elastic bands, and any other trims that hinders recycling 5x faster than manual disassembly. The low-oxygen chamber ensures no risks of fabric oxidation and recyclability rates as high as 90%.
When you hear “circular economy,” think “modular.” This shift in perspective is essential for fostering sustainable fashion and advancing circular design principles.
Photo by Ethan Bodnar on Unsplash
The importance of yields in scaling industrial textile-to-textile recycling.
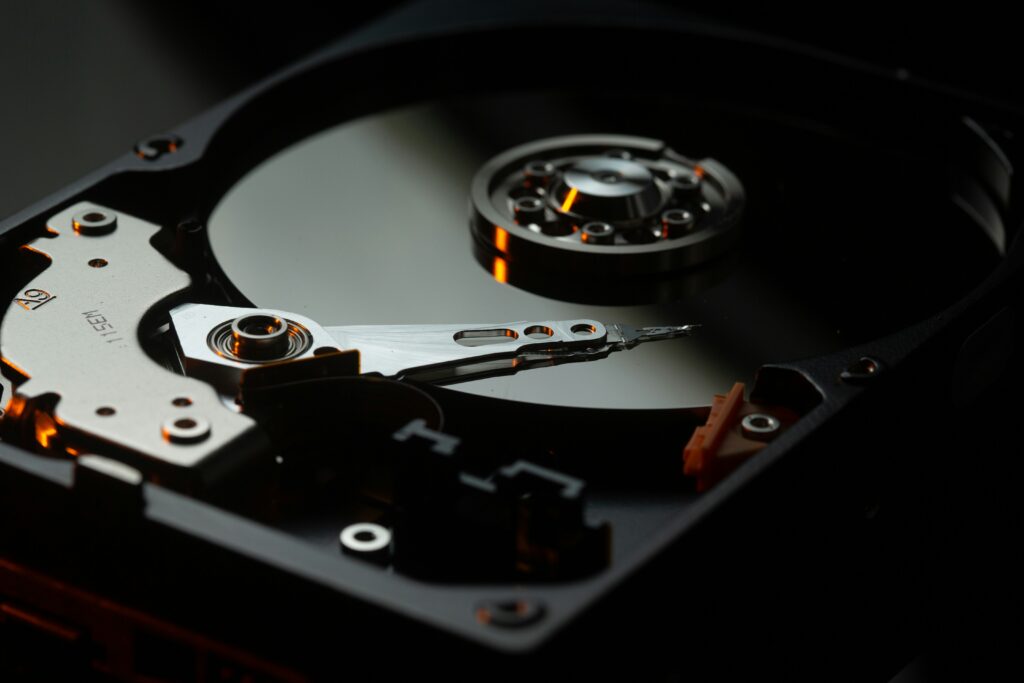
Textile recycling and circularity are becoming crucial points to be addressed for the survival of the textile industry. The surge in urgency in recent years is facilitated by the increasingly tightening regulations on handling textiles at end-of-life and the mandatory use of recycled content, as well as changing demands from critical stakeholders such as investors, media, and end-users.
In the discussions around closing the loop for the textile industry, one thing remains hidden: technology alone will not be enough. To make post-consumer textile-to-textile recycling the new norm, it needs to become profitable. And work is still required to achieve that profitability by scaling processes and increasing their efficiencies. Without tackling the low yield of current textile-to-textile recycling supply chains, recycling feedstock capacity and profit margins for textile players will remain at risk. This poses a bigger concern on achieving a closed loop at an European level, compromising EU’s future competitiveness in the market.
Big strides have been achieved in reaching the required recycled feedstock levels, yet innovative recycling technologies alone are not sufficient. Textile-to-textile recycling must evolve to be both financially viable and operationally scalable.
“Textile-to-textile recycling must evolve to be both financially viable and operationally scalable.”
When industrialising new processes, a key metric to consider is the productivity and efficiencies – i.e. yields. As argued in the study ‘The Economics of Yield-Driven Processes’ by Roger E. Bohn and Christian Terwiesch, the economic performance of production processes is heavily influenced by process yields, as these have a substantial impact on product cost, gross revenue and contribution margin. According to research on the hard disk drive (HDD) industry, the report states: “A three percentage point increase in yields can be worth about 6% of gross revenue and 17% of contribution. In fact, an eight percentage point improvement in process yields can outweigh a US$20/h increase in direct labour wages”.
In textile recycling, the level of contamination or the purity of feedstock has the most pronounced impact on yields. Some contaminations, such as elastane, are completely blocking the majority of mechanical and chemical recycling processes, while others are simply classified as waste, directly increasing overall process costs.
With 78% of apparel composed of various components, the pressing question arises: which pre-processing method maximises efficiency to achieve high yields throughout the process?
On average, trims represent 10-20% of the garment weight. Mechanical removal of trims from the textiles, also called mechanical disassembly, results in the loss up to 60% of the garment (depending on the desired output purity requirements). Manual disassembly fares slightly better, but still incurs losses ranging around 40%. For a deeper dive into the cost analysis of textile disassembly processes, refer to Resortecs’ From Waste to Profit report.
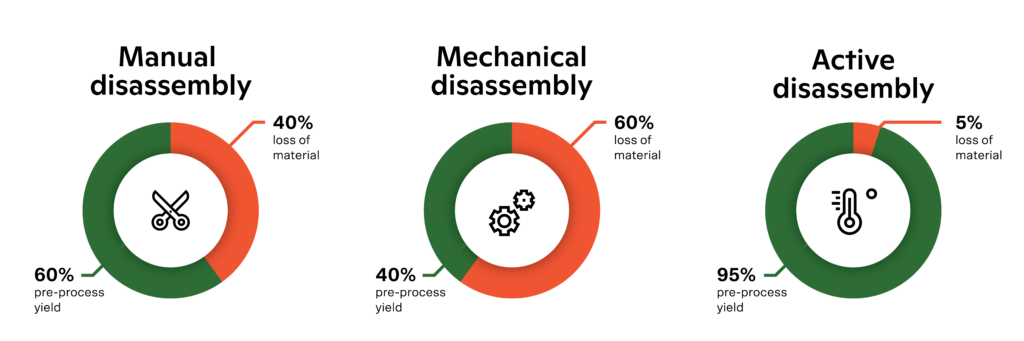
Those pre-processing yields, combined with the average yield of 80% from chemical recycling processes result in an overall post-consumer textile-to-textile recycling process with yields as low as 32%. This strikingly low yield metric underscores that price competitive recycled materials will take time to materialise. It is unsurprising that post-consumer textile-to-textile recycled materials remain costly, and why recycled PET bottles (which bypass the need for disassembly or component sorting) continue to dominate as the most popular recycled material source in the textile industry. As Leachman documented in 1996 with the Berkeley project on HDD manufacturing, a yield rate of 50% effectively doubles the costs per unit compared to those at a 100% yield.
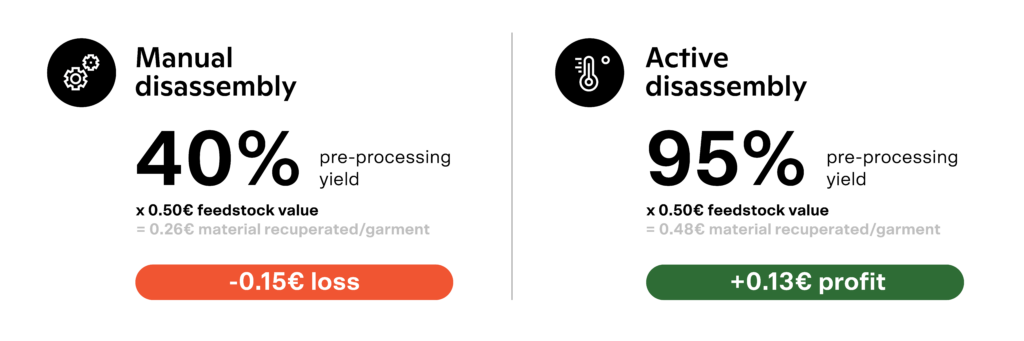
With eco-design solutions such as Resortecs, the disassembly or “de-stitching” of garments is automated, allowing for the elimination of trims and the separation of two different textiles in reusable fractions with an average material recuperation rate of 95%. This pre-processing technology not only facilitates the recycling of complex/multilayer textile products, such as denim, jackets and swimwear, but also roughly doubles the post-consumer textile recycling yields.
Despite the widespread recognition of the crucial role yields play, it is surprising how little emphasis is placed on discussions regarding efficiencies and productivity at annual textile circularity and recycling conferences. Similar to the semiconductor industry in the 1990s, prioritising yields is imperative when deciding on which technologies and processes to integrate. By increasing the pre-processing and recycling yields we will be able to industrialise textile-to-textile recycling and achieve price-competitive sustainable materials for the textile industry.
In conclusion, the journey towards mainstream textile-to-textile recycling hinges on maximising process yields and optimising efficiency across the value chain. As described above, an optimised eco-design has a significant impact on the recycling process yields and thus largely affects the price of recycled content textile brands have to pay to be compliant. This insight highlights an opportunity for textile players to switch from a reactive to proactive approach: brands must take action in the way their garments are designed to ensure low price recycled feedstock, leading to less compromise on their margins in the long-term.
By addressing pre-processing challenges and leveraging eco-design technologies like Resortecs, the industry can pave the way for price-competitive sustainable materials and drive the transition towards a circular economy in the textile sector.
Author: Cédric Vanhoeck, CEO at Resortecs
On 7 September 2023, Creamoda, EURATEX, Fedustria, and Resortecs welcomed 150 changemakers from 20 countries in Brussels to discuss the future of the fashion and textile industries.
Resortecs unveiled its latest report, “From Waste to Profit”– A Comparative Cost Analysis of Textile Disassembly Processes, available for download here, and highlighted the financial and operational benefits of Active Disassembly compared to the status quo disassembly methods – manual and mechanical.
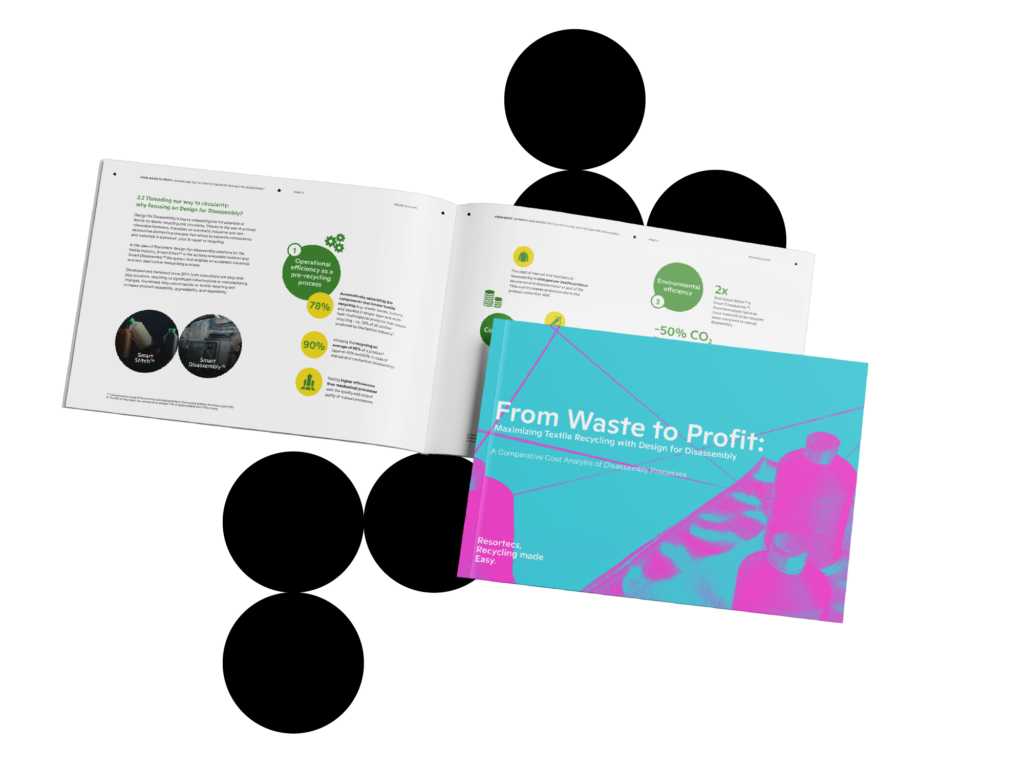
Dirk Vantyghem from Euratex gave an insightful update on the EU Textile Strategy launched last year with the aim to create a greener, more competitive textile sector. Textile products placed on the EU market need to be therefore more durable, repairable, recyclable, and to a great extent made of recycled fibers.
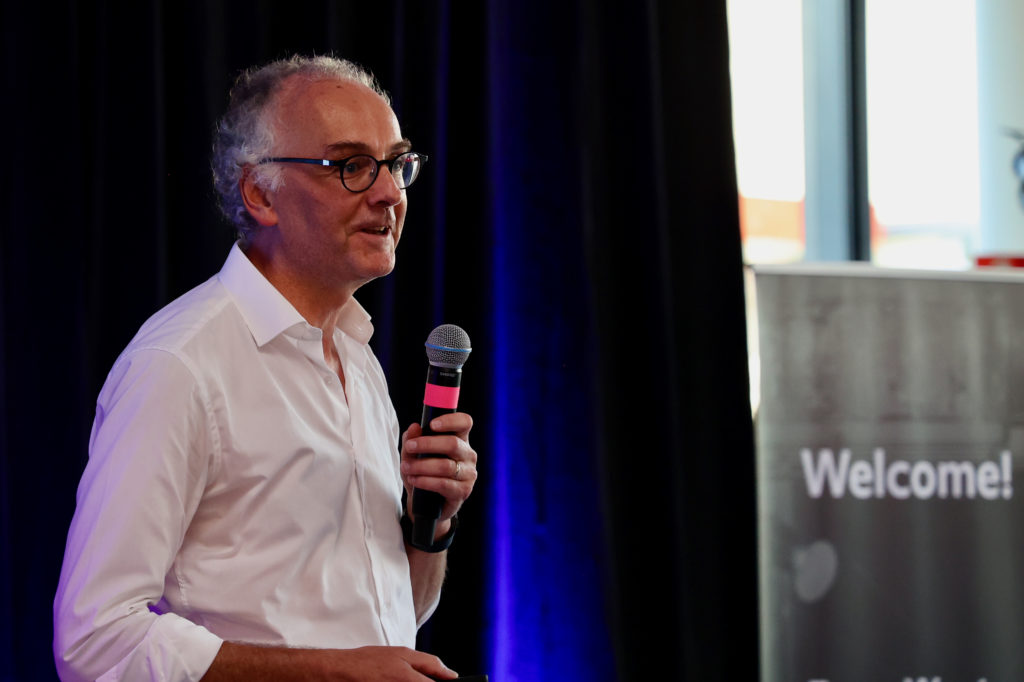
Textile recycling was highlighted as one of the solutions to drive change at scale and grow with environmental compliance, but getting there without losing the essential industrial competitiveness is of key importance for the sector.
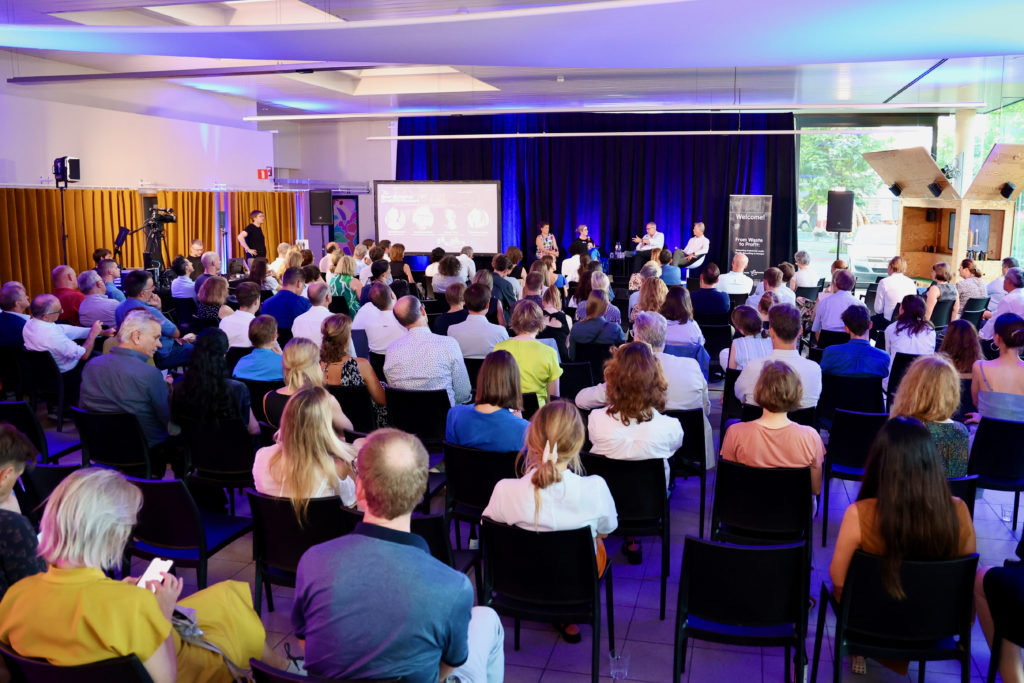
The panel discussions with Fedustria and industry leaders Concordia Textiles, Sioen, and BekaertDeslee – moderated by Christine Goulay from Sustainabelle, resulted in a number of interesting insights and testimonials on the efficiency and applicability of Active Disassembly for the textile sector.

Carl Baekelandt, Demet Tunc, Ivan Deceuninck, and Karla Basselier shared their expertise as circularity pioneers. Here are three takeaways from the insightful discussions:
1. There are now 16 legal changes focusing on the sustainability and circularity of fashion and textile companies rolling out across the EU — and more will follow.
2. 78% of all textile products require disassembly before textile-to-textile recycling.
3. Europe is becoming increasingly dependent on recycling textile waste due to 1) the shortage of raw materials and 2) the prohibition of recycled R-PET from the packaging industry for use in other sectors.
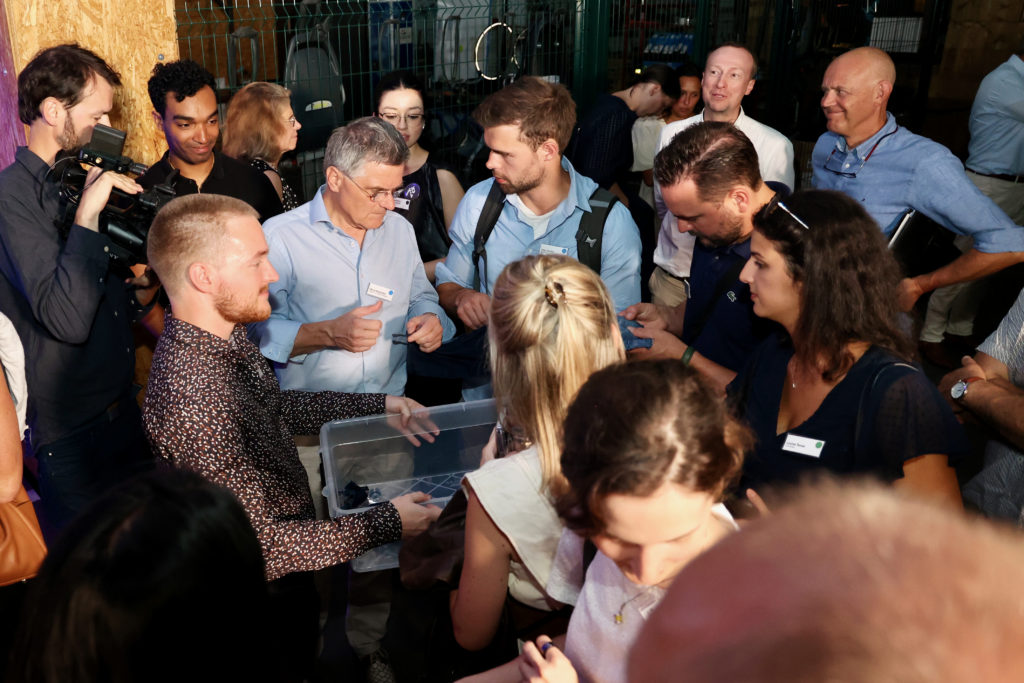
In addition, all guests also had the chance to explore Circularium and witness a live demo of Smart Stitch™ & Smart Disassembly™.
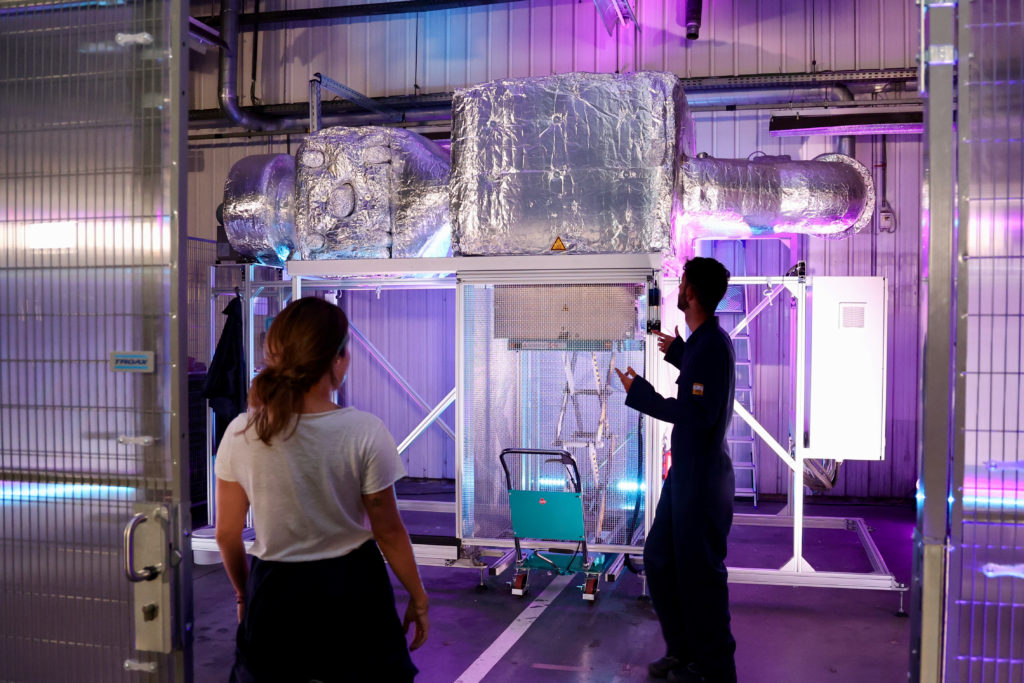
The need of collaboration to unlock industrial-scale recycling in Europe was eminent at the networking dinner & drinks at the end of the event. The connections made are testament to the commitment of all stakeholders along the textile value chain to make circularity a reality.
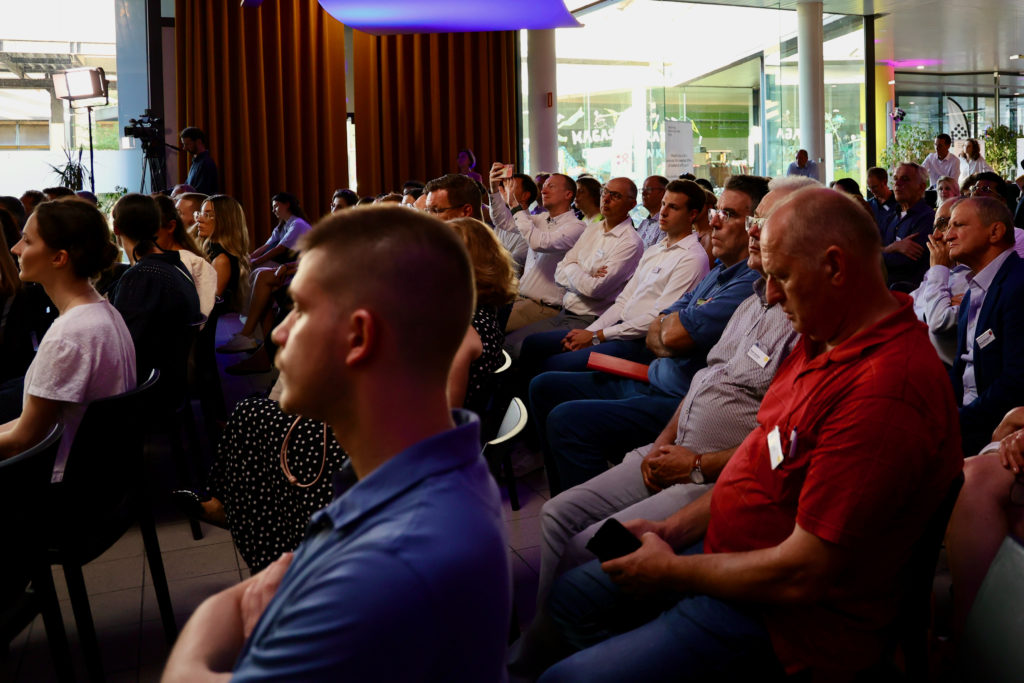
Have you already downloaded your free copy of the report ‘From Waste to Profit’ — A Comparative Cost Analysis of Disassembly Processes? Download it here.
What’s inside?
• The best-performing disassembly method for achieving maximum financial and operational efficiency.
• How different disassembly methods compare across four textile product categories: multilayer outdoor jackets, cotton trousers, aramid-based workwear, and mattress covers.
• How fashion and textile brands can transform product recycling into a source of ROI rather than costs at the end of a product’s lifecycle.
• What policymakers and brands should do to keep the European textile and fashion industries competitive.
BRUSSELS, BELGIUM – Wedze, the winter-sports brand of French giant Decathlon, partnered with Belgian innovator Resortecs to launch a fully recyclable ski jacket using the start-up’s design-for-disassembly technology.
Different from normal ski jackets, which are extremely difficult to recycle due to their complex material composition, this flagship is made of 63% recycled polyester, and 23% of the fabrics are dyed using dope dyeing – one of the most water-efficient dying techniques.
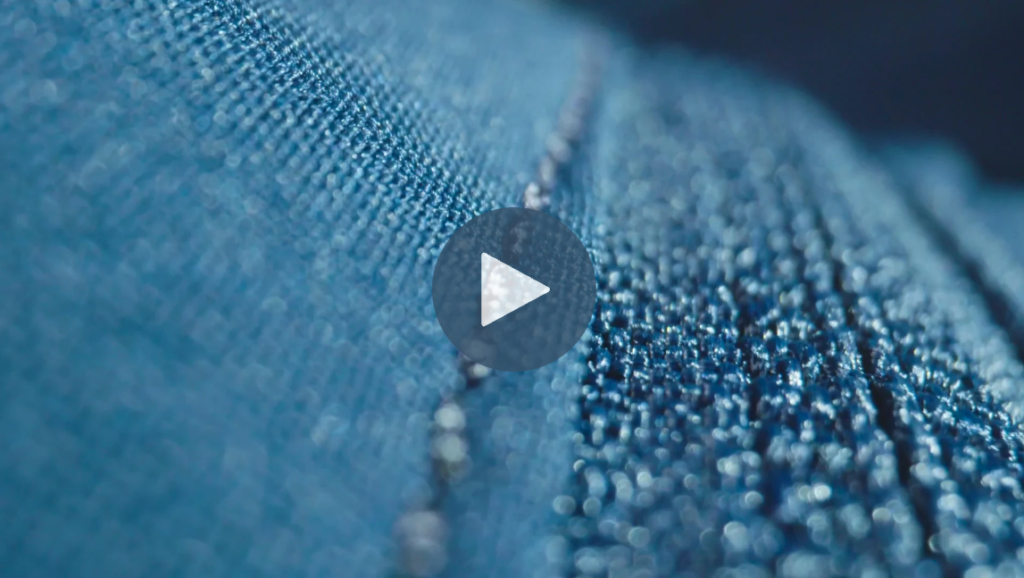
As making a completely mono-material jacket isn’t yet possible , Wedze found in Resortecs the ideal partner to bring its first fully recyclable ski jacket to life. The start-up’s Smart Stitch™ threads melt and disappear when exposed to temperatures above 190°C, ensuring that the non-recyclable zippers, press buttons and elastics bands can be easily separated from the polyester parts when it is time for recycling.
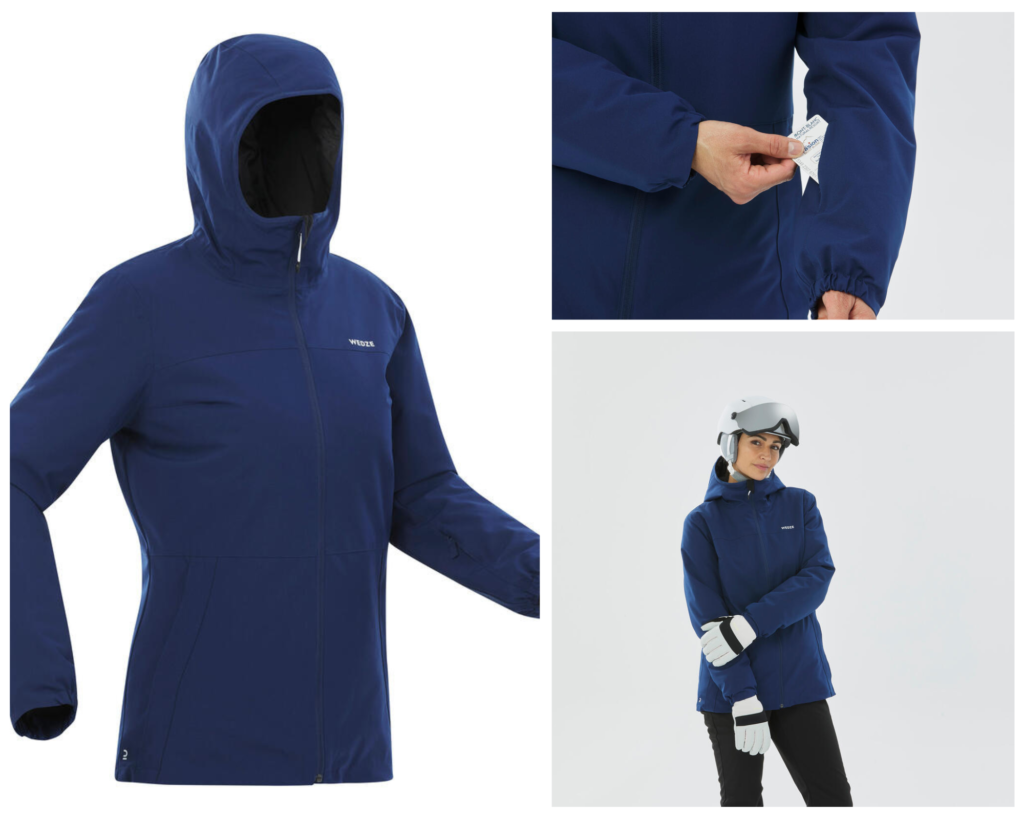
“Clients who want to join our circularity efforts can return their used jackets when they are no longer fit for use, and we’ll recycle them into new products.” Explains Fern S., Product Engineer and Sustainable Development Leader at Wedze.
“We are excited to launch a product with Wedze because, like the entire Decathlon group, they are known for their efforts to develop more sustainable products. The jacket looks great and has infinite possibilities for its next lifecycle.” – Cédric Vanhoeck, co-founder & CEO at Resortecs
Decathlon joins H&M and Bershka (Inditex Group) in our client roster and becomes the 3rd major global brand to launch products with Smart Stitch™ and Smart Disassembly™ in less than a year.
Skiers who don’t want to compromise on sustainability when hitting the slopes can find the disruptive jacket at Decathlon stores in Spain and online at www.decathlon.com for all other European markets.
Resortecs – REcycling, SORting, TEChnologieS – is an award-winning start-up that develops design-for-disassembly solutions. We drive full circularity in fashion with heat-dissolvable stitching threads and thermal disassembly systems that make recycling easy.
For further inquiries:
Davidson Leite
Communications & Branding Lead
[email protected]
BRUSSELS, BELGIUM – Brussels-based start-up Resortecs is partnering with Bershka, a global fashion brand part of the Inditex Group, to launch a new capsule collection using the start-up’s design-for-disassembly technology to facilitate recycling and upcycling.
The collaboration brings together summer and circularity in two unisex products – denim shorts and jeans – made with Resortecs’ Smart Stitch™ for easy disassembly. The products will be available online and at selected stores in 60 markets across the world as of 5 August.
Resortecs aims to boost textile recycling with two patented innovations: Smart Stitch™, heat-dissolvable stitching threads, and Smart Disassembly™, an industrial oven capable of taking apart the different components of clothing made with Smart Stitch™. This way, the start-up expects to reduce the high costs and complexity of separating different textile materials ahead of recycling.
For Bershka, this collaboration is part of Inditex’s Sustainability Innovation Hub: an open-innovation platform that works alongside start-ups, academic institutions, and tech centers to promote and scale disruptive solutions for new materials, technologies and processes that reduce the environmental footprint of fashion products and help advance towards circularity.
Founded in 2017 by Cédric Vanhoeck and Vanessa Counaert, Resortecs has already validated its solution with over 30 international fashion players:
We are thrilled to work with Bershka. Since day one, we’ve been positively
surprised by how much their team is committed to the circular transition.
The final products look great and have infinite possibilities for their next
lifecycle. – Cédric Vanhoeck, co-founder & Executive Lead
Resortecs – REcycling, SORting, TEChnologieS – is an award-winning start-up that develops design-for-disassembly solutions. We drive full circularity in fashion with heat-dissolvable stitching threads and thermal disassembly systems that make recycling easy.
For further inquiries:
Davidson Leite
Communications & Branding Lead
[email protected] | +32 0494 94 93 54
Resortecs’ innovation – the first of its kind – can process up to 1 ton of garments per day and is being tested by 30 major global fashion brands
Recently, images of the mountains of unsold clothing dumped in the Atacama Desert, in Chile, shocked the world. Each year, 34 million tonnes of textiles worth more than 400 billion euros are wasted by the fashion industry – which became a strategic target of the EU Green Deal. Behind these alarming figures are the costs and complexity of disassembly and recycling. When faced with stacks of unsold inventory, that might reach up to 40% of each season’s production, fashion brands turn to options easier and cheaper than recycling, such as landfills or incineration. If it’s up to Resortecs, however, this scenario is about to change.
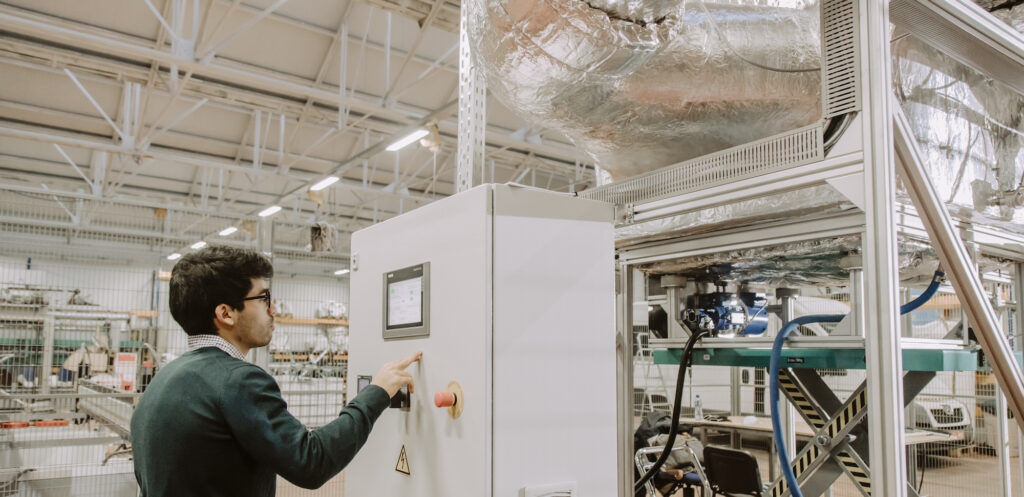
The start-up presents its first thermal disassembly system in a demonstration event for the press, politicians, investors, and industry peers in Brussels on Thursday, 09/12. The system combines heat and mechanical force to disassemble clothes stitched with Resortecs’ heat-dissolvable threads. Inside the system – a globally-patented, high-tech version of an industrial oven – the clothes are exposed to specific temperatures, making the seams disappear automatically and allowing for easy material sorting and recycling.
“The system works with little to no oxygen inside. This preserves the fabrics’ quality and prevents the clothes from burning, even when they are submitted to temperatures higher than 200° C”, explains William Allouche, Technical Lead for Disassembly and the mind behind the system’s engineering. “We’ve made sure to develop a closed-loop system to preserve the heat produced for each batch of clothes for the longest time possible. This ensures energy recovery and generates way less CO2 emissions than other heat-induced processes.”
The thermal process is 5x faster than traditional disassembly methods and enables the recycling of up to 90% of the original fabric material, instead of the usual 48% obtained after manual or mechanical disassembly. Using data to prove the impact of its innovation, Resortecs ran an externally-reviewed life-cycle assessment which shows that the process adoption could help the fashion industry cut its CO2 emissions by 50% and reduce waste generation by 80%. If the entire EU production were thermally disassembled and recycled, the fashion industry could generate 60.3 million fewer tons of CO2 and save up to € 2.3 billion per year.
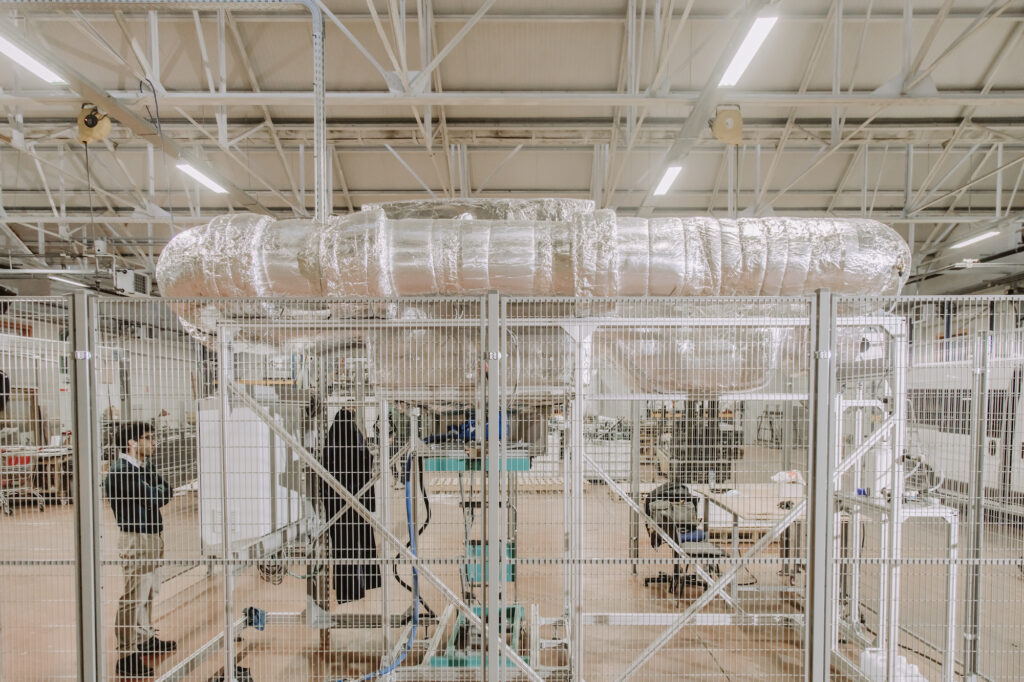
The version presented to the public is just a prototype. It can process up to 1 ton of textile per day and is being used to show first partners, such as the fast-fashion giant H&M and other 30 global fashion brands, how the start-up’s solution works. In the long term, it will be part of a network of thermal disassembly systems placed in recycling plants all over the world. The idea is to cover the globe with automatic thermal disassembly to speed up global textile recycling. Still in 2022, a second system with a larger processing capacity will come into operation. Together, both units will be able to prepare up to 13 tonnes/day of clothing for recycling, an unprecedented volume in the world.
“Everyone thinks of recycling, but no one looks at the biggest challenge to make it happen: disassembly. We saw an opportunity to optimize production while boosting up recyclability and sustainability, and we jumped on it” says founder Cédric Vanhoeck. “Brands have finally realized that there’s no way to continue producing and wasting textile as if nothing is happening with the planet. When we started 4 years ago, brands complained about the costs of sustainability, now they come to us because they understand that circularity is an investment.”
Join us.
Subscribe to our newsletter.
By subscribing, I agree with having my personal data stored and processed by Resortecs so I can receive future updates and marketing offers.
